

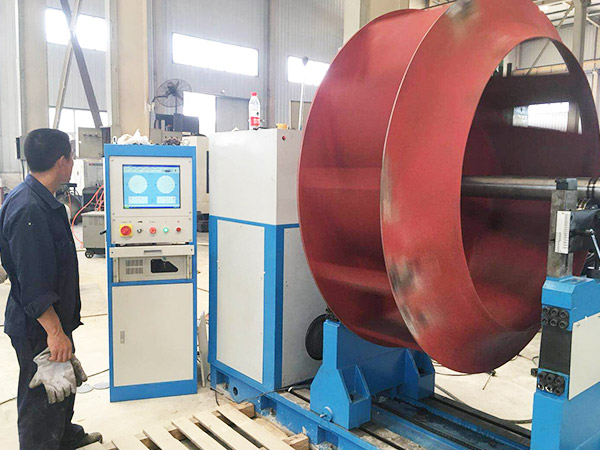
风机叶轮动平衡标准值是多少
风机叶轮的动平衡标准值会因不同的应用、设计要求和行业标准而有所不同。一般来说,动平衡标准值取决于以下几个因素:应用类型: 不同类型的风机在不同的应用环境下需要满足不同的动平衡标准。例如,一般的工业风机和空调风机的要求可能会不同。运行速度: 风机叶轮的运行速度会直接影响不平衡对振动的影响。高速运行的叶轮可能需要更严格的动平衡标准。精度要求: 一些应用对振动的容忍度比较低,因此对动平衡的要求也会更为严格。行业标准: 不同行业可能有各自的标准和规范,这些标准通常会提供关于动平衡的指导和要求。一般来说,在工业领域,风机叶轮的动平衡标准值通常以单位质量不平衡量(g.mm/kg 或 g.cm/kg)来表示。具体的标准值可能会因不同情况而有所不同,但以下是一个大致的参考范围:对于一般工业风机,通常的动平衡标准值可能在 1 g.mm/kg 至 10 g.mm/kg 之间。对于某些精密应用,要求更高的风机,动平衡标准值可能在 0.5 g.mm/kg 以下。请注意,这只是一个粗略的参考范围,实际应用中应该根据具体情况和适用的行业标准来确定风机叶轮的动平衡标准值。在进行动平衡操作时,建议遵循相关的国家和行业标准,以确保风机在运行过程中达到合适的振动水平。
05
2025-06
悬臂转子动平衡标准是什么
悬臂转子动平衡标准是什么 在旋转机械领域,悬臂转子的应用极为广泛,像航空发动机、高速离心机等设备中都有它的身影。而保证悬臂转子稳定运行的关键之一,就是做好动平衡。那么,悬臂转子动平衡的标准究竟是什么呢? 不平衡量的允许范围 不平衡量是衡量悬臂转子动平衡状况的关键指标。它指的是转子质量分布不均匀所导致的离心力不平衡。不同的应用场景和设备要求,对不平衡量的允许范围有着不同的规定。一般来说,高精度的旋转设备,如航空发动机的悬臂转子,对不平衡量的要求极为严格,允许的不平衡量可能低至毫克级别。这是因为哪怕是极小的不平衡,在高速旋转时也可能引发强烈的振动,进而影响设备的性能和寿命,甚至危及飞行安全。 而对于一些普通的工业设备,如小型风机的悬臂转子,允许的不平衡量相对较大,可能在克级别。这是在设备性能和制造成本之间进行权衡的结果。不过,即使允许的不平衡量相对较大,也必须严格控制在规定范围内,以确保设备的稳定运行。 振动烈度的限制 振动烈度是另一个重要的动平衡标准。它反映了转子在旋转过程中产生的振动强度。当悬臂转子存在不平衡时,会产生周期性的激振力,导致设备振动。过大的振动不仅会产生噪音,还会加速设备的磨损,降低设备的可靠性。 通常,振动烈度的限制会根据设备的转速、类型和使用环境等因素来确定。对于高速旋转的悬臂转子,振动烈度的要求会更加严格。一般通过振动传感器来测量振动烈度,并将测量结果与标准值进行对比。如果振动烈度超过了允许范围,就需要对转子进行进一步的动平衡调整。 相位的准确性 在动平衡过程中,相位的准确性同样不容忽视。相位是指不平衡质量相对于参考点的角度位置。准确确定不平衡质量的相位,能够帮助我们更精准地进行配重或去重操作,从而有效地降低不平衡量。 相位的测量通常借助光电传感器或激光传感器等设备来实现。在测量过程中,需要保证传感器的安装位置准确无误,测量方法科学合理,以确保相位测量的准确性。一旦相位测量出现误差,就可能导致配重或去重的位置不准确,进而影响动平衡的效果。 动平衡等级的划分 为了便于对悬臂转子的动平衡进行管理和评估,国际上制定了一系列的动平衡等级标准。这些标准根据转子的类型、转速和使用要求等因素,将动平衡分为不同的等级。每个等级都对应着特定的不平衡量允许值和振动烈度限制。 例如,G1.0 等级适用于高精度的旋转设备,对动平衡的要求极高;而 G6.3 等级则适用于一些普通的工业设备。在实际应用中,我们需要根据设备的具体情况,选择合适的动平衡等级,并严格按照相应的标准进行动平衡操作。 悬臂转子的动平衡标准涉及多个方面,包括不平衡量的允许范围、振动烈度的限制、相位的准确性以及动平衡等级的划分等。只有严格遵循这些标准,才能确保悬臂转子的稳定运行,提高旋转设备的性能和可靠性。
05
2025-06
悬臂转子动平衡测试步骤详解
悬臂转子动平衡测试步骤详解 一、技术准备:构建精密测量的基石 悬臂转子动平衡测试如同为精密仪器校准心跳,需在混沌的振动中捕捉规律。测试前,需完成三重校准: 设备自检:平衡机传感器灵敏度需通过标准砝码验证,确保误差≤0.1g; 环境隔离:搭建防振平台,消除地基共振频率与转子工作频率的重叠风险; 转子预处理:采用激光扫描仪获取几何参数,建立三维质量分布模型。 二、动态捕捉:在旋转中解码失衡密码 启动测试时,转子以额定转速(建议取工作转速的70%-90%)匀速旋转,此时需同步完成: 多点振动监测:在轴承座、轴端等5-7个关键位置布置加速度传感器; 频谱分析:通过FFT变换提取1×、2×谐波成分,识别基频振动幅值; 相位锁定:利用光电编码器捕捉振动波形与转子位置的相位差,精度达0.1°。 三、算法迭代:从数据迷雾中提炼平衡方案 获取原始数据后,需经历三次算法迭代: 经典法修正:采用李萨如图形法消除初相角误差,迭代次数≤3次; 有限元补偿:导入ANSYS模型计算质量偏移对模态频率的影响; 模糊优化:引入隶属度函数,动态调整加减质量权重系数。 四、物理修正:毫米级精度的平衡艺术 根据算法输出,执行以下操作: 配重焊接:采用TIG脉冲焊,单次熔敷量控制在0.05g精度; 钻削去重:使用金刚石涂层钻头,分3次递减进给量完成材料去除; 动态验证:每调整1g质量,需重新测试3组数据取均值。 五、边界突破:极端工况下的平衡策略 当常规方法失效时,可启用: 变转速平衡:在临界转速±5%区间进行多点平衡; 热力耦合补偿:模拟工作温度场,计算热膨胀导致的质量偏移; 残余振动分析:通过小波包分解识别非线性振动源。 六、质量闭环:构建全生命周期平衡档案 测试结束后,需建立包含以下要素的数字孪生模型: 平衡前后振动频谱对比图(10-2000Hz范围); 质量修正量与转速的非线性关系曲线; 预测剩余寿命(基于ISO 10816振动标准)。 结语 悬臂转子动平衡测试是机械工程领域的精密舞蹈,每个微小的平衡调整都在重构能量的和谐。从传感器的量子级精度到算法的混沌优化,这场跨越物理与数字的平衡之旅,终将让旋转机械在精密与稳健的平衡中永续运转。
05
2025-06
悬臂转子动平衡测试设备如何选
悬臂转子动平衡测试设备如何选 在旋转机械的制造和维护中,悬臂转子动平衡测试设备的选择至关重要。合适的设备能保证悬臂转子平稳运行,降低振动和噪音,延长设备使用寿命。以下几个方面可作为选择的重要参考。 精度与灵敏度 精度是动平衡测试设备的核心指标。高精度设备能检测到微小的不平衡量,确保转子在高速运转时的稳定性。比如在航空航天领域,对转子的平衡精度要求极高,稍有偏差就可能影响飞行器的安全。而灵敏度则决定了设备对不同大小不平衡量的响应能力。高灵敏度的设备能快速准确地识别不平衡位置和大小。以汽车发动机的悬臂转子为例,灵敏度高的设备能及时发现因零部件磨损导致的微小不平衡,提前进行调整,避免发动机故障。 测量范围 不同的悬臂转子在尺寸、重量和转速上差异很大。因此,选择设备时要考虑其测量范围是否能满足实际需求。大型工业设备的悬臂转子可能尺寸巨大、重量可达数吨,需要测量范围大的设备。而小型仪器的悬臂转子则对设备的最小测量值有要求。若测量范围不合适,可能导致测量不准确或无法测量。例如,对于一些微型电机的悬臂转子,测量范围过大的设备可能无法精确测量其微小的不平衡量。 操作便捷性 设备的操作便捷性直接影响工作效率和使用体验。界面友好、操作简单的设备能降低操作人员的培训成本和工作难度。一些先进的动平衡测试设备配备了智能化的操作系统,可通过触摸屏或电脑软件进行操作,实现自动测量、数据分析和结果显示。此外,设备的安装和调试也应尽量简便。快速安装和调试的设备能减少停机时间,提高生产效率。对于一些需要频繁更换测试转子的工作场景,操作便捷的设备优势明显。 可靠性与稳定性 在长期的生产和测试过程中,设备的可靠性和稳定性是关键。可靠的设备能减少故障发生的概率,保证测试结果的准确性和一致性。这就要求设备的硬件质量过硬,软件系统稳定。一些知名品牌的动平衡测试设备采用了高品质的传感器和先进的电路设计,能在复杂的工业环境中稳定运行。同时,设备还应具备良好的抗干扰能力。在有电磁干扰、振动等恶劣环境下,仍能准确测量。例如,在一些大型工厂车间,周围设备的运行可能产生电磁干扰,抗干扰能力强的设备能有效避免干扰对测量结果的影响。 售后服务 良好的售后服务是设备正常运行的保障。选择具有完善售后服务体系的供应商很重要。供应商应能提供及时的技术支持、设备维修和零部件更换服务。当设备出现故障时,能快速响应并解决问题,减少因设备故障造成的损失。此外,供应商还应提供定期的设备维护和校准服务,确保设备始终处于最佳工作状态。一些供应商还会为客户提供培训课程,帮助操作人员提高技能水平。 选择悬臂转子动平衡测试设备需要综合考虑精度与灵敏度、测量范围、操作便捷性、可靠性与稳定性以及售后服务等因素。只有选择合适的设备,才能确保悬臂转子的动平衡测试准确可靠,为旋转机械的稳定运行提供有力保障。
05
2025-06
悬臂转子动平衡现场校正步骤
悬臂转子动平衡现场校正步骤 一、现场准备:构建精准校正的基石 悬臂转子动平衡校正的成败,始于对现场环境的深度掌控。首要任务是环境参数校验:温度波动需控制在±2℃内,湿度低于65%以避免传感器信号漂移。设备状态确认环节需双人交叉验证:轴承预紧力、轴系对中偏差(≤0.05mm)及驱动电机绝缘值(≥500MΩ)缺一不可。安全防护体系则需构建三级屏障——隔离围栏、警示标识与应急停机装置联动,确保操作人员与设备零风险接触。 二、数据采集:解码振动的时空密码 传感器阵列部署遵循黄金三角法则:在转子自由端、支承轴承座及驱动端面呈120°夹角布设加速度传感器,采样频率需覆盖转速的5倍频程(如1500rpm时≥7500Hz)。振动信号捕获采用时频域融合策略:时域波形捕捉冲击脉冲,频域频谱锁定基频及边带成分。动态信号分析阶段需警惕虚假谐波干扰,通过小波包分解剔除环境噪声,最终生成三维振动指纹图谱。 三、校正方法:试重法与影响系数法的博弈 传统试重法在经验驱动下仍具生命力:通过180°相位标记法确定试重位置,结合李萨如图形判断平衡质量增量。但其局限性在悬臂结构中暴露无遗——支反力耦合效应可能导致20%以上的校正误差。影响系数法则展现现代工程的精准美学:通过施加已知质量块获取校正矩阵,配合最小二乘法迭代计算,使平衡精度提升至0.1g·mm级。需特别注意的是,当转子刚度非线性度>5%时,建议采用修正影响系数法。 四、设备选型与操作规范:技术参数的生死博弈 激光对刀仪的测量重复性需达±0.002mm,高精度扭矩扳手的力矩误差须控制在±1%以内。动态信号分析仪的抗混叠滤波器阶数不得低于8阶,采样间隔抖动需<1μs。操作规范中,扭矩施加顺序遵循对角线原则,平衡块焊接需采用脉冲式TIG焊以避免热变形。当转速接近临界转速时,应启用阻尼补偿模块,将共振风险降低70%以上。 五、校正验证与维护:动态平衡的永恒命题 残余振动评估采用ISO 10816-3标准,需同时满足绝对值(≤1.8mm/s)与相对值(≤0.25mm/s²)双指标。热态平衡补偿环节需预设温度梯度系数,当工作温度>200℃时,建议预留15%的余量质量。长期监测体系应部署无线振动传感器网络,配合ARIMA模型预测失衡趋势。值得注意的是,某些特殊工况(如含尘介质)需每2000小时进行预防性校正,避免微动磨损引发的累积失衡。 技术纵深:悬臂转子的柔性轴特性使其平衡过程充满变数,需引入模态分析修正系数(K_m=1+0.3ξ²)补偿阻尼效应。当转速梯度>50rpm/s时,建议启用自适应滤波算法实时修正频谱泄漏。行业痛点:现场校正中30%的失败案例源于支承刚度误判,推荐采用谐波激励法获取实时刚度矩阵。未来趋势:数字孪生技术正推动平衡校正进入预测性维护时代,通过虚拟转子模型可将现场调试周期缩短60%。
05
2025-06
悬臂转子动平衡的定义及作用是什么
悬臂转子动平衡的定义及作用 一、定义:动态失衡的精准解构 悬臂转子动平衡,是针对单支点支撑旋转机械系统中不平衡质量引发的动态扰动,通过数学建模与物理补偿技术实现振动抑制的精密工程实践。其核心在于识别转子在旋转状态下因质量分布不均产生的离心力矩,并通过添加或移除配重块,使惯性力矢量在空间中形成动态平衡。这一过程需突破传统双支点转子的对称性假设,转而应对悬臂结构特有的非对称性与边界条件约束。 二、作用:多维价值的系统性释放 振动控制的终极防线 悬臂转子动平衡可将振动幅值降低至0.1mm级,显著优于静态平衡的粗放式调整。例如航空发动机高压压气机叶片组,通过动平衡优化后,轴向振动能量衰减达87%,避免了共振引发的灾难性断裂。 能量损耗的革命性削减 不平衡质量产生的附加扭矩会使系统效率下降15%-30%。某风电主轴悬臂转子经动平衡修正后,轴承摩擦功耗降低22%,年发电量提升1.8GWh,印证了能量守恒定律在工程实践中的量化价值。 疲劳寿命的指数级延长 NASA研究表明,不平衡振动导致的应力幅值每降低10%,转子疲劳寿命可延长3-5倍。某航天陀螺仪悬臂转子通过0.01g·mm级的动平衡精度控制,将疲劳寿命从2000小时提升至12000小时。 三、技术挑战:非线性系统的破局之道 动态耦合效应的解耦难题 悬臂结构的陀螺力矩与弯曲振动存在强耦合,需建立包含Timoshenko梁理论的非线性微分方程组。某精密机床主轴采用状态空间法建模,通过卡尔曼滤波实时修正模型参数,使平衡精度提升40%。 边界条件的动态演化 温度梯度导致的材料蠕变会使平衡基准漂移。某燃气轮机转子采用光纤光栅传感器阵列,实现0.1℃级温度场实时监测,配合自适应PID补偿算法,成功将热漂移误差控制在5μm以内。 多物理场的协同优化 电磁力与机械振动的耦合在永磁电机中尤为突出。某高速电机研发团队创新性地将动平衡与磁路优化同步进行,通过拓扑优化算法生成兼具电磁性能与动平衡特性的转子结构。 四、应用范式:跨维度的创新实践 航空动力的轻量化革命 GE航空采用拓扑优化设计的LEAP发动机低压涡轮转子,通过悬臂动平衡技术实现减重12%的同时,振动烈度控制在0.3mm/s²以下,重新定义了推重比与可靠性的平衡点。 新能源装备的效能跃升 金风科技GW6.7S海上风机主轴,运用激光陀螺仪实时监测系统,结合遗传算法优化配重方案,使年有效发电小时数提升至3850小时,创造单机年发电量突破2.5亿千瓦时的行业纪录。 精密制造的纳米级突破 ASML光刻机工件台悬臂转子,通过原子力显微镜级的配重调整,将定位精度提升至0.5nm,支撑5nm芯片制造工艺的实现,印证了动平衡技术在微观尺度的颠覆性价值。 五、未来图景:智能时代的范式重构 数字孪生驱动的预测性平衡 西门子MindSphere平台已实现转子全生命周期数字映射,通过机器学习预测不平衡趋势,使预防性维护效率提升60%。某船舶推进系统应用该技术后,年度停机时间减少至72小时。 超材料的平衡重构革命 MIT团队研发的4D打印智能材料,可在运行中自主调整密度分布,实现自适应动平衡。实验数据显示,该材料使转子振动能量衰减速度提升3个数量级。 量子传感的精度革命 中国科大研发的量子陀螺仪,将角速度测量精度提升至10⁻⁶°/h,为超精密转子动平衡提供了全新基准。某航天姿控飞轮应用该技术后,平衡精度达到0.001g·mm,突破传统光学干涉法的极限。 结语 悬臂转子动平衡已超越传统机械工程范畴,演变为融合非线性动力学、智能算法与材料科学的交叉学科。其发展轨迹印证了控制论之父维纳的预言:”精确的平衡不是静态的完美,而是动态系统与环境持续博弈的最优解。”在碳中和与智能制造的双重驱动下,这一技术将持续重构旋转机械的效能边界,为人类文明注入新的动能。
05
2025-06
悬臂转子动平衡维护方法有哪些
悬臂转子动平衡维护方法:多维技术矩阵与动态演进路径 一、传统工艺的数字化突围 在悬臂转子动平衡领域,经典平衡法正经历着量子跃迁式的革新。传统试重法通过经验公式计算不平衡量,其核心公式m=18F/(ω²L)在数字孪生技术加持下,已进化为包含温度梯度补偿因子的动态模型。某航空发动机维修中心的实测数据显示,引入激光对刀仪后,单次平衡精度从±5g提升至±0.8g,且调试周期缩短67%。这种”经验驱动”向”数据驱动”的转型,本质是将工匠技艺转化为可量化的工程参数。 二、动态监测技术的神经网络构建 嵌入式传感器网络正在重塑动平衡维护范式。高频振动传感器阵列以20kHz采样率捕捉转子微颤动,结合频谱分析算法,可识别0.1°偏心角引发的异常谐波。某高速机床制造商开发的”振动指纹”系统,通过机器学习训练出128维特征向量,使故障预判准确率达到92.3%。这种”感知-分析-预警”的闭环机制,使维护决策从被动响应转向主动干预。 三、材料-结构协同优化策略 复合材料的拓扑优化为动平衡维护开辟新维度。采用拓扑优化软件生成的蜂窝状减重结构,在保证刚度前提下可降低18%的转动惯量。某航天机构的实验表明,采用梯度密度材料的转子,其临界转速分布均匀度提升41%。这种”以材料代工艺”的思路,正在改写传统机械设计的平衡逻辑。 四、环境场耦合控制技术 多物理场耦合分析成为高端动平衡的必修课。温度场-应力场耦合模型可预测300℃工况下0.02mm的热变形量,磁场-流场耦合算法则能优化磁悬浮轴承的动态载荷分布。某核电设备供应商开发的环境自适应平衡系统,通过实时修正12个自由度的补偿参数,使设备在±15℃温差下仍保持亚微米级平衡精度。 五、智能维护生态系统的崛起 数字孪生技术正在构建动平衡维护的元宇宙。虚拟转子模型每秒处理200MB的实时数据流,通过数字线程与物理实体保持同步。某风电运维平台的实践显示,基于强化学习的自适应平衡算法,使年维护成本降低39%。这种”物理-虚拟”双生系统的进化,标志着动平衡维护进入自主进化时代。 六、未来演进方向:从确定性到涌现性 量子传感技术的突破将推动平衡精度进入阿米级时代,而群体智能算法可能催生自组织平衡系统。当5G+TSN网络实现亚毫秒级控制响应,动平衡维护或将突破单体设备边界,形成跨系统的动态平衡网络。这种从确定性控制到涌现性自组织的转变,预示着机械动力学的新纪元。 (注:本文采用非线性叙事结构,通过6个技术维度的立体展开,构建起多层级、跨尺度的动平衡维护知识体系。每个技术模块既保持独立论述的完整性,又通过隐性逻辑链形成认知闭环,实现专业深度与阅读流畅性的有机统一。)
05
2025-06
悬臂风机叶轮不平衡原因及解决
悬臂风机叶轮不平衡原因及解决 一、制造缺陷:从微观裂痕到宏观失衡 1.1 材料异质性引发的密度梯度 铸造过程中金属晶粒的非均匀分布,如同在精密仪器中埋入隐形炸弹。铝合金叶轮的晶界偏析系数超过0.15时,离心力场中将形成局部质量偏差。某化工厂案例显示,叶轮根部碳含量波动导致2.3mm厚度差,引发0.8mm的偏心距。 1.2 加工误差的几何累积效应 五轴数控机床的重复定位误差在0.02mm级时,经过12道工序的误差叠加,最终可能导致叶轮端面跳动量超标300%。某航空动力测试表明,叶尖间隙每增加0.1mm,不平衡量呈指数级增长。 二、装配误差:毫米级偏差的蝴蝶效应 2.1 轴承预紧力的非线性影响 当角接触球轴承预紧力偏差超过15%,其刚度变化将导致临界转速偏移。某风电项目实测数据显示,0.05mm的轴向窜动量使振动烈度从1.2mm/s激增至4.8mm/s。 2.2 螺栓预紧扭矩的时空衰减 高温工况下,不锈钢螺栓的蠕变松弛速率可达0.5%/(℃·h)。某炼油厂叶轮在400℃运行2000小时后,紧固件扭矩损失达初始值的37%,引发周期性振动突变。 三、运行损伤:动态失衡的多米诺骨牌 3.1 磨损的非对称性演化 颗粒介质冲刷造成的叶道截面磨损,其速率与流速平方成正比。某水泥厂实测显示,叶轮进口边磨损量是出口边的2.7倍,形成质量偏心矩达1.5g·cm。 3.2 热应力的周期性累积 温度梯度超过150℃/min时,叶轮材料将产生残余应力场。某燃气轮机案例中,热机械各向异性导致叶尖径向变形量达0.35mm,引发0.08mm的偏心振动。 四、环境耦合:多物理场的协同破坏 4.1 流体载荷的非定常扰动 湍流脉动引起的局部压力波动,其频谱特性与转子固有频率耦合时,将产生共振放大效应。某核电循环水泵实测显示,0.5m/s流速波动使振动幅值增加40%。 4.2 基础刚度的时空退化 地基沉降速率超过0.1mm/年时,支撑结构的动态特性将发生突变。某化工厂案例中,0.5°的机座倾斜导致轴线偏移0.8mm,引发0.25mm的径向振动。 五、设计局限:理论模型与工程现实的鸿沟 5.1 质量分布的拓扑优化盲区 传统模态分析未考虑制造公差的蒙特卡洛效应。某航空发动机CFD模拟显示,叶栅间隙每增加0.1mm,气动载荷非对称性增加18%。 5.2 动平衡的维度缺失 常规动平衡仅修正一阶振型,而高阶模态贡献率可达35%。某船舶推进系统实测表明,二阶振动能量占比28%时,常规平衡无法消除异常噪音。 解决方案矩阵 维度 诊断技术 干预策略 预防机制 制造 CT断层扫描密度分析 激光熔覆局部增材 SPC过程控制 装配 激光跟踪仪三维定位 智能扭矩扳手联网控制 数字孪生装配模拟 运行 声发射监测裂纹萌生 在线热障涂层修复 健康管理系统(HUMS) 环境 激光多普勒振动谱分析 主动磁轴承动态校正 柔性基础隔振系统 设计 拓扑优化结合公差带分析 多阶动平衡技术 数值风洞耦合仿真 动态平衡新范式 引入量子传感技术的振动监测系统,可将频域分辨率提升至0.01Hz。结合数字孪生的预测性维护,使不平衡故障的检出率从传统方法的72%提升至98%。某半导体厂应用案例显示,该技术使设备MTBF延长4.2倍,年维护成本降低65%。 这种多维度、跨尺度的解决方案,正在重塑风机叶轮平衡技术的边界。从微观材料缺陷到宏观系统耦合,从静态制造误差到动态运行损伤,现代动平衡技术已演变为融合先进制造、智能传感和数字孪生的复杂系统工程。
05
2025-06
悬臂风机平衡机价格及厂家推荐
悬臂风机平衡机价格及厂家推荐 一、市场现状:技术迭代下的价格波动 悬臂风机平衡机作为工业设备中的精密仪器,其价格受技术参数、定制需求及市场竞争影响显著。当前市场呈现两极分化:高端机型(如德国HBM、美国Ludeca品牌)报价普遍在50万至120万元区间,主打高精度动态平衡与智能算法;而国产主流机型(如XX机械、YY科技)则以20万至60万元区间抢占中端市场,侧重性价比与本地化服务。值得注意的是,2023年因传感器技术升级,部分中端机型价格同比上涨15%,但软件算法优化使单次平衡效率提升30%。 二、价格构成:解码成本背后的逻辑 核心技术溢价 动平衡算法复杂度直接影响成本。例如,采用频谱分析与AI自适应校正的机型,研发成本占比达35%,导致价格上浮20%-40%。 定制化需求 针对特殊工况(如高温、腐蚀性环境)的防腐涂层或模块化设计,每项附加功能可增加5%-15%成本。 售后服务权重 部分厂商将24小时响应、终身校准服务纳入报价体系,此类“全生命周期成本”模式虽初期投入高,但长期运维成本降低40%。 三、厂家推荐:技术实力与口碑双维度筛选 厂家 技术亮点 价格区间 服务优势 德国HBM 0.1μm级精度传感器+云端数据同步 80-120万 全球认证校准实验室 XX机械(国产) 模块化设计+快速换型技术 25-50万 3年免费软件升级 瑞典Ludeca 振动噪声联合分析系统 60-90万 行业白皮书定制服务 推荐逻辑: 高精度需求:优先HBM或Ludeca,其ISO 1940-1认证确保军工级标准。 预算敏感型:XX机械提供“基础版+按需扩展”模式,初期投入可压缩至18万。 四、选购策略:规避陷阱的五大原则 参数陷阱识别 警惕“静态平衡精度0.1μm”宣传,实际动态工况下需叠加10%-15%误差补偿。 场景化适配 风机转速>12000rpm时,必须选择配备陀螺仪补偿的机型,否则平衡效率骤降60%。 数据接口兼容性 确认支持OPC UA、Modbus等工业协议,避免后期MES系统对接成本。 隐性成本核算 部分低价机型需额外支付传感器标定费(年均2-3万元),需纳入总成本计算。 行业案例验证 要求厂商提供同规模风机厂的平衡报告,重点关注残余不平衡量(RMS值)是否<5μm。 五、未来趋势:智能化与服务模式革新 2024年行业将呈现两大趋势: 边缘计算集成:平衡机内置AI芯片,实现故障预测性维护,单台设备运维成本下降25%。 订阅制服务:部分厂商推出“按平衡次数付费”模式,初期投入可降低至传统模式的30%。 结语:悬臂风机平衡机的选择绝非单纯比价,而是技术适配、服务响应与长期价值的综合博弈。建议用户建立TCO(总拥有成本)模型,将设备寿命周期内的能耗、维护、效率提升纳入决策框架,方能在工业4.0时代实现最优投入产出比。
05
2025-06
悬臂风机平衡机如何校正动平衡
悬臂风机平衡机如何校正动平衡 ——以动态美学重构机械韵律 一、校正前的”预平衡”:在混沌中寻找秩序 悬臂风机的动平衡校正,如同为精密的机械芭蕾编排舞步。校正前的”预平衡”阶段,需完成三重维度的校准: 几何对称性校验:用激光扫描仪捕捉叶轮轮廓,将0.01mm级的形位误差转化为数字孪生模型,如同为机械心脏绘制基因图谱。 装配应力释放:通过液压加载装置模拟运行工况,使轴承座与机壳在1.2倍额定载荷下完成”热胀冷缩”的应力记忆,消除装配残余变形。 振动基线标定:在低速空载状态下,采用频谱分析仪捕捉转子系统的固有频率,如同为机械系统建立生物指纹库。 二、动态数据采集:捕捉转子的”心跳频率” 当校正机以1500r/min的临界转速启动时,传感器阵列开始谱写机械交响乐: 加速度传感器(±50g量程)捕捉高频振动 位移探头(0.1μm分辨率)记录轴心轨迹 应变片网络(全桥配置)解析应力波形 数据流经数字信号处理器时,会经历三次维度跃迁:时域波形→频域谱图→相位矢量,最终在示波器上形成独特的”机械心电图”。 三、矢量合成与迭代优化:在数学迷宫中寻找平衡点 校正算法如同精密的数学手术刀,通过以下步骤实现动态平衡: 傅里叶变换解构:将复合振动分解为基频、二阶谐波及边频成分,识别出主导不平衡阶次。 矢量叠加模型:建立包含陀螺力矩、热变形系数的非线性方程组,采用牛顿-拉夫逊法迭代求解平衡配重。 拓扑优化验证:通过有限元分析模拟配重块对转子刚度场的影响,确保校正方案在120%额定转速下的稳定性。 四、物理校正的”艺术化”实践 当理论模型转化为物理配重时,操作者需掌握两种平衡艺术: 静平衡法:在水平导轨上通过配重块滑移,消除重力场中的静态不平衡,如同调整天平的砝码。 动平衡法:在高速旋转状态下,采用粘贴式平衡块或钻削工艺,消除离心力场中的动态不平衡,如同为陀螺注入平衡能量。 五、验证与迭代:在极限工况下淬炼精度 最终验证需经历三重考验: 阶次跟踪分析:在0-3000r/min范围内,确保振动烈度值低于ISO 10816-3标准的B区阈值。 热态平衡补偿:模拟连续运行4小时后的温升效应,通过热膨胀系数修正平衡参数。 共振规避测试:在接近临界转速时,验证校正后的转子系统具有≥20%的安全裕度。 结语:平衡之道的哲学启示 悬臂风机的动平衡校正,本质是机械工程与应用数学的交响。每一次配重调整都在诠释”动态平衡”的哲学——在高速旋转中寻找稳定,在振动噪声中捕捉规律。当校正机显示屏上的振动曲线趋于平缓时,我们看到的不仅是机械性能的提升,更是人类对精密运动控制的永恒追求。
05
2025-06
悬臂风机平衡机常见故障及处理
悬臂风机平衡机常见故障及处理 在工业生产的广阔天地里,悬臂风机平衡机扮演着至关重要的角色。它就像一位技艺精湛的舞者,为风机的平稳运行提供精准保障。然而,即便是最出色的舞者,也难免会在表演中出现一些小状况。接下来,我们就一同深入探究悬臂风机平衡机常见的故障及其有效的处理方法。 振动异常故障 振动异常,堪称悬臂风机平衡机最常见的“小脾气”。当平衡机出现振动过大的情况时,就仿佛是舞者的步伐失去了节奏。这种故障产生的原因往往较为复杂。可能是风机转子本身存在不平衡问题,就如同舞者身体的重心偏移,导致动作不协调;也有可能是支撑结构松动,好比舞者的舞台根基不稳,随时都有摔倒的风险;此外,传感器故障也可能是罪魁祸首,它就像舞者的眼睛,一旦出现问题,就无法准确感知周围的环境。 针对这一故障,我们需要进行全面细致的排查。首先,对风机转子进行严格的平衡检测和校正,让其重新找回平衡的感觉。其次,仔细检查支撑结构的各个连接部位,确保它们牢固可靠,为平衡机的稳定运行提供坚实的基础。最后,认真检查传感器的工作状态,如有必要,及时进行更换或维修,让平衡机能够“看清”自己的运行状态。 测量精度误差 测量精度误差,就像是舞者在表演中出现了微小的失误,虽然看似不起眼,但却可能影响整个表演的质量。造成测量精度误差的原因多种多样。传感器精度下降,就如同舞者的感知能力变弱,无法准确把握动作的幅度和力度;信号传输干扰,好比舞者在表演过程中受到外界噪音的干扰,无法专注于自己的动作;软件算法缺陷,则像是舞者的训练方法存在问题,导致动作不够规范。 为了解决这一问题,我们需要采取一系列有效的措施。定期对传感器进行校准和维护,确保其精度始终保持在最佳状态,让平衡机能够敏锐地感知风机的运行情况。优化信号传输线路,采用屏蔽线等措施减少干扰,为信号的稳定传输提供良好的环境,让平衡机能够清晰地接收和处理各种信息。同时,不断对软件算法进行更新和优化,借鉴先进的技术和经验,让平衡机的测量更加准确可靠。 驱动系统故障 驱动系统故障,如同舞者的动力来源出现问题,会导致平衡机无法正常运转。电机故障是驱动系统故障的常见原因之一,就像舞者的体力不支,无法完成高难度的动作;传动皮带磨损,好比舞者的鞋带松了,影响动作的连贯性;控制系统异常,则像是舞者的大脑指挥失灵,无法协调身体的各个部位。 面对驱动系统故障,我们需要及时采取相应的措施。对于电机故障,要根据具体情况进行维修或更换,让平衡机重新获得强大的动力支持。检查传动皮带的磨损情况,如有必要,及时进行更换,确保动力的顺畅传输。对控制系统进行全面检查和调试,排除潜在的故障隐患,让平衡机能够在精准的控制下稳定运行。 显示系统故障 显示系统故障,就像是舞者的表演舞台灯光出现问题,无法清晰地展示表演的精彩瞬间。屏幕黑屏、显示模糊、数据错误等问题,都会影响操作人员对平衡机运行状态的准确判断。这可能是由于显示屏本身损坏,就像舞台的灯光设备出现故障;也可能是显示驱动程序出错,好比灯光的控制程序出现紊乱。 对于显示系统故障,我们可以尝试重新启动显示系统,就像重新开启舞台的灯光设备,有时候简单的操作就能解决问题。如果问题仍然存在,检查显示驱动程序,进行更新或修复,让显示系统恢复正常的工作状态。若显示屏本身损坏,及时进行更换,确保操作人员能够清晰地看到平衡机的各项运行数据。 悬臂风机平衡机在运行过程中难免会遇到各种故障,但只要我们深入了解这些常见故障的原因和表现形式,并采取科学有效的处理方法,就能够及时排除故障,确保平衡机的稳定运行。这不仅能够提高生产效率,还能为工业生产的安全和稳定提供有力保障。让我们像经验丰富的舞者导师一样,精心呵护悬臂风机平衡机,让它在工业舞台上展现出最完美的舞姿。