

刚性转子动平衡:原理与实践
- 分类:行业新闻
- 作者:申岢编辑部
- 来源:上海申岢动平衡机制造有限公司
- 发布时间:2025-03-26
- 访问量:224
刚性转子动平衡是旋转机械领域的关键技术,直接影响设备运行安全与使用寿命。当转子以角速度ω旋转时,微小的质量偏心会产生与转速平方成正比的离心力,这种动态不平衡力会引发剧烈振动,甚至导致轴承磨损、结构疲劳等严重后果。本文深入探讨刚性转子动平衡的核心原理与技术实现。
一、动平衡的物理本质
在旋转坐标系中,不平衡质量产生的离心力矢量构成平面力系。根据达朗贝尔原理,动平衡的充分必要条件是惯性力系的主矢和主矩同时为零。这意味着转子不仅要满足静平衡条件(Σm_i r_i = 0),还必须满足力矩平衡条件(Σm_i r_i l_i = 0),其中l_i表示质量微元轴向位置。
临界转速是动平衡的重要考量参数。当转子工作转速接近其临界转速时,系统会进入共振区,此时微小不平衡量会被急剧放大。实验数据显示,转子在临界转速区运行时,振动幅值可达正常工况的5-8倍,这要求动平衡精度必须提高一个数量级。
与静平衡相比,动平衡需要解决三维空间中的力偶平衡问题。典型的例子是存在180°相位差的两个不平衡质量,这种配置虽满足静平衡条件,但旋转时会产生周期性力矩,导致转子发生摆动振动。
二、动平衡实施方法
双平面平衡法是工程实践中的标准解决方案。选择两个与惯性主轴垂直的校正平面,通过矢量分解将任意分布的不平衡量等效为这两个平面内的当量不平衡。理论计算表明,只要校正平面间距不小于转子长度的1/3,即可有效消除所有阶次的振动模态。
影响系数法建立了振动响应与试重之间的定量关系。通过两次不同相位的试重实验,测量各轴承座处的振动变化,构建影响系数矩阵。该方法的优势在于能够自动补偿系统支承刚度等参数的影响,实测平衡精度可达0.1g·mm/kg以上。
现场动平衡技术采用相位跟踪与频谱分析相结合的方式。使用激光转速计同步采集键相信号,结合FFT分析提取工频振动分量。最新研究显示,基于自适应滤波的在线平衡系统可将平衡过程缩短至30分钟内,且无需停机操作。
三、工业应用与精度控制
汽轮机转子平衡要求最为严苛,API标准规定残余不平衡量应小于1.5G·mm/kg。某600MW机组低压转子通过六次迭代平衡,最终将轴承振动控制在25μm以下,符合ISO10816-3的优良等级。这需要采用高精度去重设备,控制每次去重深度误差不超过0.01mm。
微型电机转子平衡面临独特挑战,其直径通常小于50mm,转速可达10万转/分。微陀螺效应导致传统配重法失效,此时多采用激光烧蚀去重技术,配合空气轴承支撑,可实现0.001g·mm的平衡精度。研究证明,该方法可将硬盘马达的噪声降低12dB以上。
未来发展方向聚焦于智能平衡系统,集成有限元仿真与实时监测数据。德国某实验室已研制出自适应平衡头,内置压电作动器可在0.1秒内调整配重位置,特别适用于变工况运行的航空发动机转子。理论预测这类系统可将维护周期延长3-5倍。
刚性转子动平衡技术的发展始终与工业需求紧密相连。从早期的试重法到现代激光平衡系统,平衡精度提升了三个数量级。随着MEMS传感器和人工智能技术的融合,下一代自平衡转子系统有望实现全生命周期动态平衡,这将是旋转机械领域的重要突破。当前研究热点集中在非线性振动补偿和不确定工况下的鲁棒控制算法,这些进展将推动动平衡技术进入智能化新纪元。
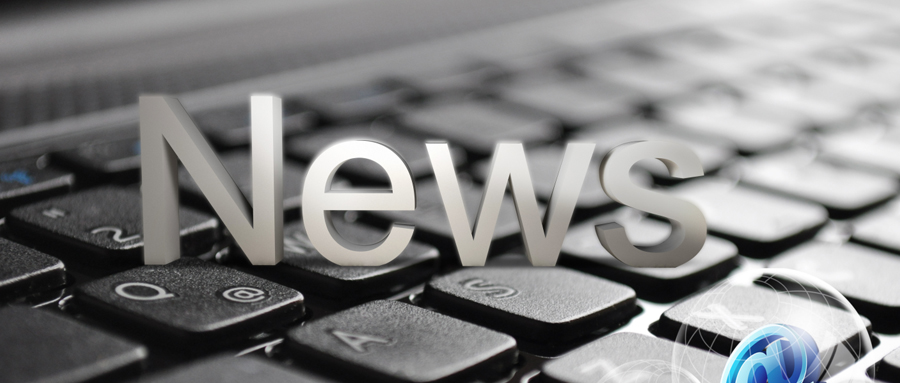