

整体动平衡技术:让机械运转更精准的秘密
- 分类:行业新闻
- 作者:申岢编辑部
- 来源:上海申岢动平衡机制造有限公司
- 发布时间:2025-03-24
- 访问量:98
在现代化工业生产中,精密机械的稳定运行直接影响着产品质量和生产效率。当一台价值千万的高端数控机床因主轴振动超标导致加工精度下降,当风力发电机组的叶片因微小失衡缩短使用寿命,这些场景都在印证一个真理:机械系统的动态平衡是工业文明的基石。整体动平衡技术正是在这种需求背景下应运而生,成为保障现代工业设备稳定运行的核心技术之一。
一、动态平衡技术的革新突破
传统动平衡方法主要采用离线平衡方式,将旋转部件单独拆卸进行平衡校正。这种方式存在明显局限性:平衡后的部件重新装配时可能产生新的误差,无法真实还原设备实际运行状态。整体动平衡技术突破性地将整个运转系统作为平衡对象,通过先进的传感网络实时采集设备在真实工况下的振动数据。
系统采用模块化传感器阵列,能够在设备全速运转状态下同步采集多维度振动信号。高精度位移传感器可捕捉微米级的轴系偏移,三向加速度计则精确记录空间振动矢量。这些实时数据通过工业总线传输至智能分析系统,构建出设备的三维振动模型。
核心算法融合了有限元分析和机器学习技术,不仅能准确识别主要失衡相位,还能预测次级振动源的潜在影响。这种智能诊断能力使得平衡校正方案不再是简单的质量配平,而是综合考虑材料特性、装配间隙、温度形变等多因素的系统优化。
二、智能化系统的技术优势
现代整体动平衡系统采用非接触式激光测量技术,在设备连续运转过程中即可完成数据采集。这种在线平衡方式避免了传统方法必须停机拆卸的弊端,特别适合连续生产线的维护需求。测量精度可达0.1μm级别,相当于头发丝直径的千分之一。
智能补偿系统能够自动生成最优配重方案,指导操作人员在指定相位添加精确质量块。某些先进系统已实现自动配重功能,通过伺服控制的配重滑块在转子表面自动移动定位,整个过程无需人工干预,将平衡效率提升80%以上。
在航空航天领域,某型号航空发动机采用该技术后,转子系统的不平衡量降低了92%,使用寿命延长3倍;汽车制造企业的电机生产线应用后,产品不良率从1.2%降至0.05%。这些数据印证了智能化动平衡技术的实际价值。
三、跨行业应用图谱
在能源装备领域,大型汽轮机组、水轮发电机的转子系统长度超过20米,整体动平衡技术能有效控制这种超长轴系的弯曲振动。某水电站应用后,机组振动值从120μm降至25μm,达到国际水电联盟的优质标准。
精密制造行业对动平衡要求更为严苛,半导体晶圆设备的真空主轴必须达到G0.4级平衡精度。整体动平衡系统通过环境振动隔离技术和频域滤波算法,成功实现纳米级的振动控制,为芯片制造提供基础保障。
随着工业4.0的发展,新一代动平衡系统开始集成数字孪生技术。通过建立设备的虚拟镜像,工程师可以在数字空间模拟不同工况下的振动特性,预判潜在失衡风险。这种预测性维护模式将设备可靠性提升到全新高度。
在工业设备向着高速化、精密化发展的今天,整体动平衡技术正在重新定义机械系统的性能边界。从微米级医疗设备到百吨级发电机组,这项技术持续突破物理极限,为现代制造业提供着看不见的精准保障。随着智能传感技术和人工智能算法的不断进步,未来的动平衡系统将具备更强的自学习和自适应能力,为工业设备开启零振动时代奠定技术基础。
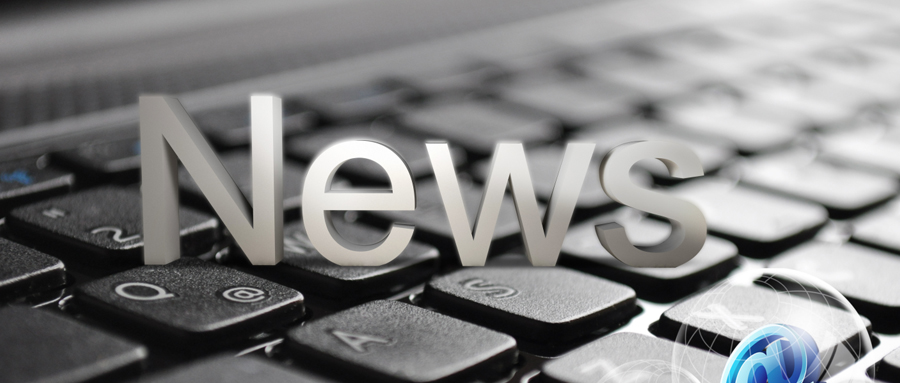