

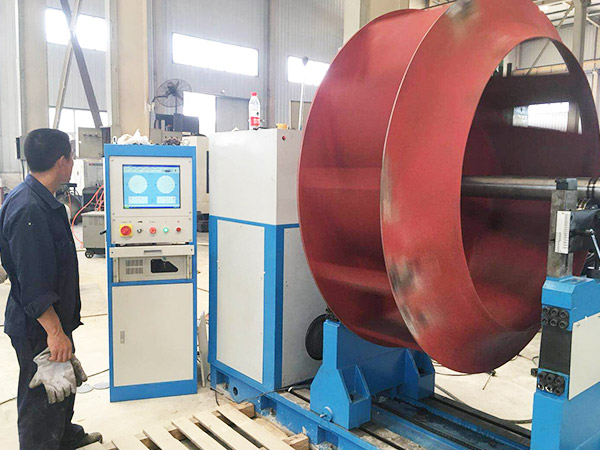
风机叶轮动平衡标准值是多少
风机叶轮的动平衡标准值会因不同的应用、设计要求和行业标准而有所不同。一般来说,动平衡标准值取决于以下几个因素:应用类型: 不同类型的风机在不同的应用环境下需要满足不同的动平衡标准。例如,一般的工业风机和空调风机的要求可能会不同。运行速度: 风机叶轮的运行速度会直接影响不平衡对振动的影响。高速运行的叶轮可能需要更严格的动平衡标准。精度要求: 一些应用对振动的容忍度比较低,因此对动平衡的要求也会更为严格。行业标准: 不同行业可能有各自的标准和规范,这些标准通常会提供关于动平衡的指导和要求。一般来说,在工业领域,风机叶轮的动平衡标准值通常以单位质量不平衡量(g.mm/kg 或 g.cm/kg)来表示。具体的标准值可能会因不同情况而有所不同,但以下是一个大致的参考范围:对于一般工业风机,通常的动平衡标准值可能在 1 g.mm/kg 至 10 g.mm/kg 之间。对于某些精密应用,要求更高的风机,动平衡标准值可能在 0.5 g.mm/kg 以下。请注意,这只是一个粗略的参考范围,实际应用中应该根据具体情况和适用的行业标准来确定风机叶轮的动平衡标准值。在进行动平衡操作时,建议遵循相关的国家和行业标准,以确保风机在运行过程中达到合适的振动水平。
19
2025-06
风机叶轮动平衡应选立式还是卧式
各位风机小达人,你们好呀!今天咱来唠唠风机叶轮动平衡的事儿。你知道吗,在风机的使用和维护里,叶轮动平衡那可是相当关键的一环,就像给风机装了个“稳定器”,能让它运行得又稳又顺,还能让风机的使用寿命蹭蹭往上涨。但是呢,在做叶轮动平衡的时候,有个大难题摆在咱面前:是选立式动平衡,还是卧式动平衡呢?接下来咱就好好掰扯掰扯。 先说说立式动平衡,这就好比让叶轮“站”起来做检查。它的优点那是杠杠的!对于那些短粗的叶轮来说,立式动平衡简直就是“私人订制”。想象一下,一个矮墩墩的叶轮,要是让它“躺”着做动平衡,就跟喝醉酒似的摇摇晃晃,根本没法好好检测。但要是把它“立”起来,就像个小战士一样稳稳当当,检测起来自然更精准。而且啊,立式动平衡设备占地小,对于场地有限的工厂来说,这简直就是“救星”,能给企业省下不少地儿呢! 不过呢,立式动平衡也有它的小毛病。对于长叶轮,它就有点“掉链子”了。长叶轮“站”着的时候,因为自身重力的影响,可能会像个没骨头的软面条一样弯曲变形,这样检测结果就不准啦。而且,立式动平衡操作挺复杂,得专业技术人员来弄,这人力成本一下子就上去了。 再看看卧式动平衡,这就像是让叶轮“躺”着做检查。它特别适合长叶轮,长叶轮“躺”着的时候,能像根笔直的钢梁一样保持形状,检测出来的结果更可靠。而且,卧式动平衡操作简单,一般工人培训一下就能上手,人力成本也就降下来了。 但是,卧式动平衡也有不足。它的设备占地大,需要宽敞的场地,对于场地紧张的企业来说,这简直就是个“大麻烦”。而且,对于短粗叶轮,卧式动平衡的检测效果可能不如立式动平衡,短粗叶轮“躺”着的时候,可能会固定不牢,晃来晃去,影响检测准确性。 那到底咋选呢?其实啊,这得根据叶轮的具体情况和企业的实际需求来定。要是叶轮短粗,企业场地又小,那立式动平衡就是更好的选择,既能保证检测准确,又不占地方。要是叶轮长,企业场地宽敞,卧式动平衡可能更合适,能让长叶轮检测得更准,操作还简单。 在风机叶轮动平衡的选择上,没有绝对的好坏,只有更适合。企业得综合考虑叶轮形状、场地条件、人力成本这些因素,做出最明智的决策。这样才能让风机叶轮动平衡检测更准确,让风机运行得更稳定高效!各位觉得是不是这个理儿呢?
19
2025-06
风机叶轮动平衡怎么做步骤图解
各位机械小能手们!今天咱来聊聊风机叶轮动平衡咋做,我给大家好好唠唠。 首先是准备工作。在给风机叶轮做动平衡之前,得把家伙事儿都备齐了。啥百分表、扳手、配重块,这些都得安排上。百分表就像个小侦探,能精准测出叶轮摆动的情况;扳手呢,就是拆卸和安装部件的小能手。而且工作场地得安全又干净,不能有啥杂物出来捣乱。还得好好检查下风机,瞅瞅叶轮有没有明显的损坏,像叶片有没有裂纹、变形啥的。要是有损坏,那得先把叶轮修好或者换一个,不然可没法接着干。 接着是初始检测。先把风机停下来,让它老老实实待着。然后用百分表测量叶轮的径向和轴向跳动。测径向跳动的时候,把百分表触头抵在叶轮外圆上,慢慢转动叶轮,这百分表的指针就跟跳舞似的乱动,把最大和最小的读数记下来,它们的差值就是径向跳动量。轴向跳动测量也差不多,把触头放叶轮端面上测就行。通过这些测量,咱就能知道叶轮现在有多不平衡,给后面的调整提供依据。要是跳动量超过正常范围,那就说明这叶轮不平衡得厉害,得重点照顾了。 然后是确定不平衡位置。这时候就得请出动平衡仪这个大功臣了。把它装在风机上,启动风机让它转起来。动平衡仪就开始采集叶轮运转时的振动数据,一通分析处理后,就能告诉咱叶轮不平衡的位置和程度。有时候,也可以用试重法。先在叶轮某个位置加上一个已知重量的配重块,再启动风机看看振动咋变。要是振动变小了,说明加配重块的方向离不平衡位置不远;要是振动变大了,那就赶紧换个位置接着试,不断尝试,直到找出准确位置。 再然后就是添加或去除配重。确定好不平衡位置,就可以开始调整啦。要是叶轮偏重,就得去掉点重量。可以用打磨的方法,在偏重的地方轻轻磨掉点金属,但可千万别磨过头了,不然叶轮强度就不行了。要是叶轮偏轻,就得加配重。把合适重量的配重块用焊接或者螺栓固定的方式装在偏轻的位置。装的时候可得保证牢固,不然叶轮一转,配重块掉下来可就麻烦大了。添加或去除配重后,再启动风机,用动平衡仪或者再测下跳动量,看看叶轮平衡咋样。要是还没达到理想效果,那就接着重复上面的步骤,接着调整,直到叶轮的振动和跳动量都在正常范围为止。 最后是最终检查。完成调整后,再用百分表测下叶轮的径向和轴向跳动,保证跳动量符合要求。同时,仔细看看添加或去除配重的地方,有没有松动、裂纹啥的问题。还得让风机试运行一下,观察它在不同转速下的运行情况,听听有没有奇怪的声音,感受下振动是不是明显变小了。只有这些检查都过了,确认一切正常,风机叶轮的动平衡工作才算大功告成。 通过上面这些步骤,咱就能让风机叶轮的动平衡调整得妥妥当当,让风机更稳定、高效地运行啦!大家都学会了吗?
19
2025-06
风机叶轮动平衡操作流程说明
风机叶轮动平衡操作流程说明 一、操作前的精密准备 (1)环境校准 在启动动平衡机前,需确保车间温度稳定在20±5℃,湿度低于65%。操作台面需用激光水平仪校准至误差≤0.1mm/m,避免地基共振干扰测量精度。 (2)设备预检 对动平衡机进行空载试运行,重点检测: 主轴转速波动率≤0.5% 传感器灵敏度校准误差<0.2% 数据采集系统时基误差≤1μs (3)叶轮预处理 使用工业内窥镜检查叶轮表面,清除积尘后喷涂示踪剂标记关键节点。对叶片进行超声波探伤,确保无裂纹缺陷。 二、动态平衡实施流程 阶段1:基准定位 采用三点定位法安装叶轮: 以叶轮中心为原点建立笛卡尔坐标系 通过磁性表座固定径向基准环 使用百分表测量端面跳动量,要求≤0.08mm 阶段2:振动谱分析 启动动平衡机至额定转速(建议分级提速至工作转速的120%),采集以下数据: 时域波形:观察是否存在冲击脉冲 频谱特征:识别1×/2×/3×工频谐波 相位角:记录振动矢量方向(精度±1.5°) 阶段3:配重优化 根据傅里叶变换结果,采用最小二乘法计算: 径向配重:W=√(W1²+W2²+2W1W2cosθ) 角度修正:θ=arctan[(W2sinθ2-W1sinθ1)/(W2cosθ2-W1cosθ1)] 推荐使用激光焊接配重块,单次添加量控制在叶轮质量的0.15%以内。 三、质量控制要点 (1)多频段验证 在80%、100%、110%转速下分别测试,确保: 振动烈度≤ISO 10816-3标准B区 轴心轨迹呈稳定椭圆,无偏心涡动 (2)热态补偿 对高温叶轮实施冷态平衡时,需引入热膨胀系数修正: ΔW=α·ΔT·W0 其中α为材料线膨胀系数,ΔT为温差 (3)数据存档 建立包含以下要素的电子档案: 平衡前后振动频谱对比图 配重位置三维坐标数据 设备运行日志(含环境参数) 四、异常处理指南 当出现以下情况时需立即停机排查: 振动幅值突增>50% 频谱出现非整数倍谐波 轴心轨迹呈现香蕉形畸变 常见故障树分析: 叶片不对称磨损→调整配重位置 轴承间隙超标→更换精密级轴承 基础共振→加装隔振平台 五、智能化升级方向 (1)数字孪生应用 构建叶轮有限元模型,通过ANSYS Workbench进行模态分析,预判不平衡响应。 (2)AI辅助诊断 部署卷积神经网络(CNN)对振动信号进行模式识别,实现故障类型自动分类。 (3)远程监控系统 采用5G+边缘计算架构,实现实时振动数据云端分析,平衡建议响应时间<30秒。 本操作流程融合经典机械原理与现代传感技术,通过多维度质量控制体系,可使风机效率提升8-12%,轴承寿命延长30%以上。建议每累计运行2000小时或更换叶轮后重新校准平衡参数,以维持设备最佳运行状态。
19
2025-06
风机叶轮动平衡校正步骤有哪些
风机叶轮动平衡校正步骤有哪些 在风机的运行过程中,叶轮的动平衡至关重要。若叶轮存在不平衡问题,会导致风机振动加剧、噪音增大,严重时甚至会影响风机的使用寿命和性能。以下为您详细介绍风机叶轮动平衡校正的步骤。 准备工作 在进行动平衡校正之前,充分的准备工作必不可少。首先,要对风机叶轮进行全面的清洁,去除表面的灰尘、油污等杂质,这些杂质可能会影响测量的准确性。同时,仔细检查叶轮是否有损坏、变形等情况,若发现问题,需及时进行修复或更换。此外,还需准备好专业的动平衡设备,如动平衡仪等,并确保设备正常运行,精度符合要求。同时,要准备好合适的加重块和必要的工具,如扳手、卡尺等。 安装传感器 安装传感器是获取准确测量数据的关键步骤。将振动传感器牢固地安装在风机的轴承座上,确保其能够准确地检测到风机的振动信号。转速传感器则要安装在合适的位置,以便能够精确测量叶轮的转速。在安装过程中,要注意传感器的安装方向和角度,严格按照设备的使用说明书进行操作,确保传感器安装正确,信号传输稳定。 初始测量 开启风机,使其在正常工作转速下稳定运行。通过动平衡仪采集叶轮的振动数据和转速数据。记录下振动的幅值和相位,这些数据将为后续的平衡校正提供重要依据。在测量过程中,要确保风机运行稳定,避免外界干扰因素对测量结果的影响。多次测量取平均值,以提高测量的准确性。 计算不平衡量 根据初始测量得到的数据,使用动平衡仪内置的算法或专业的计算软件,精确计算出叶轮的不平衡量的大小和位置。这一步需要专业的知识和经验,以确保计算结果的准确性。同时,要考虑到叶轮的结构特点和工作条件,对计算结果进行合理的修正。在计算过程中,要仔细核对各项参数,避免出现计算错误。 加重或去重 根据计算得到的不平衡量,选择合适的方法进行校正。如果不平衡量较小,可以采用加重的方法,将合适的加重块准确地安装在叶轮上计算确定的位置。加重块的安装要牢固可靠,避免在运行过程中脱落。若不平衡量较大,则可能需要采用去重的方法,如通过磨削、钻孔等方式去除叶轮上多余的质量。在去重过程中,要严格控制去除的量和位置,避免对叶轮的结构造成损坏。操作完成后,再次进行测量,检查校正效果。 重复校正 一次校正可能无法完全达到理想的平衡效果,因此需要重复上述步骤,直到叶轮的振动幅值降低到允许的范围内。每一次校正后,都要对测量数据进行仔细分析,判断校正是否有效。如果振动幅值仍然较大,需要重新计算不平衡量,调整加重或去重的方案,再次进行校正。在重复校正过程中,要有耐心和细心,逐步优化校正效果。 最终检验 当叶轮的振动幅值达到规定的标准后,进行最终检验。关闭风机,再次检查加重块是否安装牢固,叶轮上是否有其他异常情况。然后重新启动风机,在不同的转速下进行运行测试,确保风机在各种工况下都能稳定运行,振动和噪音符合要求。只有通过最终检验,才能认为风机叶轮的动平衡校正工作圆满完成。 风机叶轮动平衡校正需要严格按照上述步骤进行操作,每一个环节都至关重要。只有这样,才能确保风机叶轮的平衡精度,提高风机的运行效率和可靠性,延长风机的使用寿命。
19
2025-06
风机叶轮动平衡校正的具体步骤是什么
风机叶轮动平衡校正的具体步骤是什么 一、前期准备:构建精准校正的基石 设备状态诊断 通过目视检查叶轮表面裂纹、腐蚀及装配松动,使用游标卡尺测量叶片厚度均匀性,确保机械结构无先天缺陷。 记录风机型号、转速范围、功率参数及历史振动数据,为校正方案提供决策依据。 环境与工具配置 在无振动干扰的封闭车间内操作,温度控制在15-30℃,湿度低于70%以避免传感器信号漂移。 准备激光测振仪、电子天平(精度0.01g)、平衡块焊接机及专用校正夹具,确保工具精度等级高于ISO 1940-1标准。 二、安装与校准:构建动态基准 叶轮刚性固定 采用弹性支撑装置隔离地基振动,通过液压千斤顶将叶轮轴线倾斜0.5°后复位,消除轴承预紧力对测量的干扰。 传感器精密对准 在叶轮径向对称位置安装两个压电加速度传感器,使用激光校准仪确保探头与叶轮表面垂直距离误差<0.1mm。 启动低速空转(500rpm)验证传感器信号一致性,通过频谱分析确认基频幅值差<5%。 三、振动数据采集:捕捉动态特征 多工况测量策略 在500rpm、1000rpm、额定转速三个阶梯转速下采集振动数据,每个工况持续120秒以消除瞬态干扰。 采用时域分析(均方根值)与频域分析(FFT变换)结合,识别不平衡振动(1×频率幅值占比>60%)。 异常数据处理 当发现振动相位角突变或谐波成分异常时,执行轴承间隙检测与轴系对中校验,排除非平衡因素干扰。 四、平衡量计算:数学建模与迭代优化 矢量合成法应用 基于双面平衡原理,通过公式: G_2 = rac{G_1 cdot r_1}{r_2} cdot cos( heta_2 - heta_1)G 2 = r 2 G 1 ⋅r 1 ⋅cos(θ 2 −θ 1 ) 计算二级校正平面的平衡量,其中G_1G 1 为一级校正质量,r_1, r_2r 1 ,r 2 为校正半径, hetaθ为相位角。 动态补偿策略 对于高阶不平衡(如偶不平衡),采用三次谐波补偿法,在叶轮两端对称增加0.5g质量块以抵消离心力矩。 五、校正实施:精准干预与验证 配重工艺选择 在不锈钢叶轮上采用钻孔去重法,使用数控钻床以0.1mm步进精度控制去重量; 对铝合金叶轮粘贴环氧树脂平衡块,固化后进行动平衡复测。 闭环验证流程 校正后重复测量振动值,要求ISO G2.5等级下振动速度≤4.5mm/s(10-1000Hz)。 通过雨流计数法分析振动冲击频次,确保叶轮在20年设计寿命内疲劳强度达标。 六、特殊场景应对:突破常规局限 柔性转子校正 对长径比>0.5的叶轮,采用模态分析法确定临界转速区间,避开共振区进行分段平衡。 在线平衡技术 在役风机采用便携式平衡仪,通过频闪仪实时捕捉振动相位,实现停机时间<2小时的快速校正。 结语 风机叶轮动平衡校正是一场精密的力学博弈,从微观裂纹检测到宏观振动控制,每个环节都需融合工程直觉与数学严谨性。通过多维度数据交叉验证与动态补偿策略,最终实现叶轮旋转状态从混沌到和谐的蜕变,为风机系统注入持久稳定的动力脉搏。
19
2025-06
风机叶轮动平衡校正费用多少
各位风机小主们!你们有没有想过,给风机叶轮做动平衡校正得花多少钱呢? 风机这玩意儿用处可大啦,工厂车间通风得靠它,矿井换气也少不了它。不过这风机用久了,叶轮就可能“闹脾气”,变得不平衡了,这时候就得给它做动平衡校正。那校正费用到底多少呢?这还真没个准数,得看好多因素。 首先,叶轮大小对费用影响老大了。小叶轮校正起来就像小孩子过家家,比较容易,用的设备和材料也少,费用也就低,几百块钱可能就搞定啦。但大叶轮校正可就像打一场硬仗,难度直线上升,得用更大更复杂的设备,校正时间还长,费用自然就高得离谱,好几千甚至上万都有可能。打个比方,普通家用小型风机的叶轮校正,两三百块可能就行;可大型工业风机的叶轮校正,说不定得花三五千呢! 校正精度要求也特别关键。要是精度要求不高,校正过程就跟玩似的简单,费用也就低。但要是需要高精度校正,那就得用更先进的设备和技术,校正的时候还得反复测量和调整,成本蹭蹭往上涨。比如说,一般工业生产用的风机,精度要求没那么高,校正费用可能两千左右;但像航空航天领域那种对精度要求极高的特殊行业,风机叶轮校正费用可能要好几万,这差距简直比天还大! 还有啊,地区不同,校正费用也有很大差别。在经济发达的大城市,人力成本、场地租金都高得吓人,校正费用也跟着水涨船高。而在一些经济没那么发达的地方,各方面成本低,费用就便宜不少。像在北上广这样的大城市,风机叶轮动平衡校正可能比一些中小城市贵一两千呢。 风机的类型不同,校正费用也不一样。不同类型的风机,叶轮的结构和材质有区别,校正的难度和方法也不同。就像离心风机和轴流风机,校正方式不一样,费用也有差异。离心风机的叶轮校正可能相对复杂一些,费用可能比轴流风机高个几百块。 要是你想知道具体的风机叶轮动平衡校正费用,最好找专业的校正公司咨询。他们会根据你风机的实际情况,给出准确的报价。不过在选择校正公司时,可不能只看价格,还得看看公司的技术水平、服务质量和口碑,这样才能保证校正效果,让风机能正常、稳定地运行。咋样,现在大家心里有数了吧?
19
2025-06
风机叶轮动平衡校正需要拆卸吗
风机叶轮动平衡校正需要拆卸吗 在风机的运行过程中,叶轮动平衡校正十分关键。它能有效减少振动、降低噪音、延长风机使用寿命。然而,一个经常困扰大家的问题是:风机叶轮动平衡校正需要拆卸吗?接下来,我们就深入探讨这个问题。 可选择不拆卸的情况 当风机叶轮的结构和工作环境允许时,不拆卸校正有着显著优势。首先,不拆卸能节省大量时间。拆卸风机叶轮是一项复杂的工作,要先停止风机运行,再拆除连接部件、管道等。而不拆卸校正,只需简单准备,就能快速开展校正工作,大大缩短了停机时间,对生产连续性要求高的企业意义重大。 其次,不拆卸校正可降低成本。拆卸过程可能损坏一些零部件,重新安装还需额外人力和物力。不拆卸校正避免了这些潜在损失和额外支出,有效降低了校正成本。 再者,对于一些大型或安装位置特殊的风机,拆卸难度极大。例如安装在高楼顶部或狭小空间内的风机,拆卸操作空间有限,风险高。不拆卸校正则能避免这些难题,通过专业设备和技术,在现场直接完成校正。 需要拆卸的情况 有些情况下,拆卸风机叶轮进行动平衡校正是必要的。如果叶轮表面有大量污垢、磨损或损坏,不拆卸难以对其进行全面检查和处理。污垢堆积会影响叶轮质量分布,导致不平衡;磨损和损坏部位会改变叶轮的动力学特性,只有拆卸后才能进行修复或更换。 另外,当风机内部结构复杂,不拆卸无法准确测量叶轮的各项参数时,也需要进行拆卸校正。精确的参数测量是动平衡校正的基础,只有获取准确数据,才能进行精确校正。 决策依据 判断是否拆卸风机叶轮进行动平衡校正,要综合多方面因素。风机的类型和结构是重要因素之一。小型、结构简单的风机,拆卸相对容易,可根据实际情况决定是否拆卸;大型、结构复杂的风机,拆卸困难,应优先考虑不拆卸校正。 叶轮的损坏程度也很关键。轻微不平衡且表面状况良好的叶轮,可尝试不拆卸校正;损坏严重的叶轮,必须拆卸检查和修复。 生产计划和停机时间同样不可忽视。生产任务重、停机时间有限的企业,应尽量选择不拆卸校正;有充足停机时间的企业,则可根据具体情况灵活选择。 风机叶轮动平衡校正是否需要拆卸,没有固定答案,要根据实际情况权衡利弊。在实际操作中,应咨询专业的动平衡机技术人员,他们能根据风机具体状况,制定最佳校正方案,确保风机安全、稳定运行。
19
2025-06
风机叶轮动平衡校验的常见问题有哪些
风机叶轮动平衡校验的常见问题有哪些 一、安装误差与定位偏差 动平衡校验的初始环节常因安装误差导致数据失真。例如,叶轮轴心线与校验机旋转轴心线的微小偏移(
19
2025-06
风机叶轮动平衡现场校正方法
风机叶轮动平衡现场校正方法 ——从机械振动的”隐形舞伴”到精准控制的艺术 一、现场校正的”三重门”:环境勘测、数据采集与动态建模 环境勘测:平衡精度的隐形门槛 温度梯度:叶轮材料热膨胀系数差异可能导致0.1mm级偏心量变化 振动源隔离:采用液压升降平台+磁性耦合器,阻断地基共振传递 湿度控制:在沿海风电场使用防潮传感器,避免碳纤维叶轮吸湿变形 数据采集:多维度振动指纹解析 三轴加速度计阵列:沿叶轮径向布置6点,捕捉10-500Hz频段振动 相位锁定技术:通过激光编码器同步旋转角度与振动波形 智能滤波算法:小波包分解消除齿轮箱啮合频干扰 动态建模:虚拟叶轮的数字孪生 有限元模型迭代:基于ANSYS Workbench建立12阶模态分析 误差补偿矩阵:融合温度-应力-转速多变量非线性方程组 二、动态校正技术矩阵:从传统配重到智能算法 传统配重法的现代演绎 钻孔-焊接复合工艺:在钛合金叶根预埋磁性配重块 激光熔覆修复:单次校正精度达±0.02g·mm 柔性材料动态补偿 智能流体配重环:通过压电阀实时调节硅油分布 形状记忆合金:-50℃~200℃工况下保持0.05mm形变精度 数字孪生驱动的预测性校正 LSTM神经网络:提前72小时预测偏心量变化趋势 数字孪生体:在虚拟空间完成98%的校正方案验证 三、现场实施的”五维控制法则” 转速控制悖论 低速校正(50rpm):消除轴承游隙影响 高速验证(1500rpm):捕捉气弹耦合效应 配重位置的拓扑优化 基于拓扑学的非对称配重:在叶根/叶中/叶尖建立3维平衡场 多目标优化算法:最小化配重质量与结构强度约束 残余振动的”蝴蝶效应”抑制 主动质量阻尼器:在轮毂内置0.5kg可移动配重块 振动模态解耦:通过频域滤波分离1阶/2阶不平衡振动 四、典型案例:某5MW海上风机的极限挑战 工况:台风后叶片损伤修复 难点:盐雾腐蚀导致的配重块脱落风险 方案: 开发环氧树脂-碳纳米管复合粘接剂 采用无人机搭载激光干涉仪进行高空校正 建立海上平台振动基准点补偿模型 成果:振动幅值从12.3mm/s降至1.8mm/s,达到ISO 10816-3 A级标准 五、未来趋势:从被动校正到主动控制 智能材料革命 电致伸缩陶瓷:实现0.1μs级响应的动态平衡 自修复聚合物:在-40℃环境下自动修复微裂纹 数字孪生生态构建 边缘计算节点:在风机本地完成校正方案实时生成 区块链存证:建立配重历史的不可篡改数字档案 人机协同新范式 AR增强现实:工程师通过透视眼镜实时叠加振动云图 数字孪生体自主决策:在台风预警时自动启动应急平衡程序 结语:平衡之道的本质 风机叶轮动平衡校正不仅是机械精度的较量,更是对复杂系统动态特性的深刻理解。当我们在现场拧紧最后一颗配重螺栓时,实际上是在与旋转机械的混沌运动博弈,在确定性与随机性之间寻找最优解。这种平衡艺术,终将随着智能技术的进化,演变为风电装备自主健康管理的新范式。
19
2025-06
风机叶轮动平衡配重块安装位置
各位机械小达人们!今天咱来聊聊风机叶轮动平衡配重块安装位置,这可是让旋转更稳定的秘密哟! 为啥配重块的位置这么重要呢?你想想啊,你转一个不均匀的陀螺,它会左摇右摆,还嘎吱嘎吱响,说不定“哐当”一下就倒了。风机叶轮就跟这陀螺似的,转起来的时候,哪怕有一丁点儿重量不一样,那都能震得翻天覆地。配重块就像给陀螺贴了“平衡贴纸”,找准位置这么一弄,整个系统就稳如老狗啦! 选安装位置有4个关键原则: “对称法则”:这就跟给跷跷板两边加砝码一样,配重块一般装在叶轮直径对称的地方。要是叶轮左边重了10克,右边对应位置就得加10克的配重块。 “黄金分割点”:别往叶轮边缘那些尖儿上装,要选叶片和轮毂连接的“黄金分割点”。这儿既能把震动抵消得明明白白,又不会把叶轮结构弄坏。 “动态测试法”:专业技师就跟医生拿听诊器似的,监测震动频率。仪器“嘀——”声最密的时候,那就是最佳安装位置,就像根据心跳调药一样。 “环境适应原则”:潮湿环境就选防水胶固定的配重块,高温车间就用耐热合金的。这就跟根据天气选衣服一样,配重块也得“入乡随俗”。 常见误区和解决方案来啦: 误区1:随意粘贴。把配重块像创可贴似的随便贴在叶轮表面,震动可能就跑别的地儿去了。正确做法是用专业胶水,粘得严丝合缝的。 误区2:追求“完美对称”。太追求绝对平衡,能耗会蹭蹭往上涨。就像跑步膝盖不用完全对称,留5%的自然震动反而更耐用。 误区3:忽视季节变化。冬天金属收缩,夏天膨胀,配重块松紧度得像调琴弦一样定期微调。建议每季度用游标卡尺量一量。 提升安装效果有3个实用技巧: “分层校正法”:先用小号配重块大概调一下,再慢慢加重。就像调色先打底,再加点细节。 “振动标记法”:在叶轮表面贴个特殊油膜,启动后震动最厉害的地方会留下印子,那儿就是要“补救”的地方。 “动态观察法”:安装好让风机空转10分钟,用手机慢动作拍叶轮旋转轨迹。要是有“拖尾”现象,就得重新给配重块找位置。 长期维护也有黄金法则: 每月“体检”:用磁性测厚仪查查配重块粘合度,就跟给牙齿拍X光似的。 季度“对话”:把每次调整的重量记下来,弄个“平衡日志”,方便发现规律问题。 年度“焕新”:就算没啥明显震动,也建议每年换一次配重块,免得老化掉下来。 总之,安装配重块不只是个技术活,更是一门平衡的艺术。它就像给旋转的星球装了引力锚点,让每片叶片都能稳稳地转。记住哈,真正的平衡不是把差异全弄没,而是让差异乖乖听话。下次听到风机稳稳运转的声音,说不定你就会想起那些默默守护平衡的小金属块啦!