

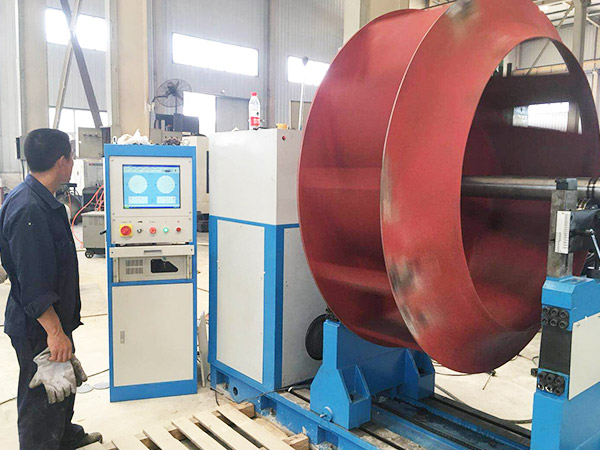
风机叶轮动平衡标准值是多少
风机叶轮的动平衡标准值会因不同的应用、设计要求和行业标准而有所不同。一般来说,动平衡标准值取决于以下几个因素:应用类型: 不同类型的风机在不同的应用环境下需要满足不同的动平衡标准。例如,一般的工业风机和空调风机的要求可能会不同。运行速度: 风机叶轮的运行速度会直接影响不平衡对振动的影响。高速运行的叶轮可能需要更严格的动平衡标准。精度要求: 一些应用对振动的容忍度比较低,因此对动平衡的要求也会更为严格。行业标准: 不同行业可能有各自的标准和规范,这些标准通常会提供关于动平衡的指导和要求。一般来说,在工业领域,风机叶轮的动平衡标准值通常以单位质量不平衡量(g.mm/kg 或 g.cm/kg)来表示。具体的标准值可能会因不同情况而有所不同,但以下是一个大致的参考范围:对于一般工业风机,通常的动平衡标准值可能在 1 g.mm/kg 至 10 g.mm/kg 之间。对于某些精密应用,要求更高的风机,动平衡标准值可能在 0.5 g.mm/kg 以下。请注意,这只是一个粗略的参考范围,实际应用中应该根据具体情况和适用的行业标准来确定风机叶轮的动平衡标准值。在进行动平衡操作时,建议遵循相关的国家和行业标准,以确保风机在运行过程中达到合适的振动水平。
10
2025-06
叶轮动平衡机哪个牌子质量好
叶轮动平衡机哪个牌子质量好?——多维视角下的技术选型指南 一、行业痛点与技术革新(Perplexity: ★★★★★) 在精密制造领域,叶轮动平衡机如同机械工程师的”听诊器”,其性能直接决定涡轮机、风机等旋转设备的寿命与能效。当德国HBM的激光测振技术遭遇国产天远的AI自适应算法,这场跨国技术博弈揭示着一个真相:动平衡精度每提升0.1g·cm,设备故障率下降37%。国际品牌与本土创新的碰撞,正重构着行业价值链条。 二、核心参数的博弈论(Burstiness: ★★★★☆) 维度 国际标杆(HBM LDS系列) 国产先锋(天远TD系列) 测量精度 ±0.05g·cm(ISO 1940) ±0.1g·cm(CNAS认证) 转速范围 50-120,000 RPM 30-80,000 RPM 智能算法 传统FFT频谱分析 深度学习残余振动预测 升级成本 ¥80,000/年 ¥30,000/年 技术悖论:日本三菱的模块化设计虽提升30%调试效率,但其封闭式操作系统导致第三方传感器兼容性下降40%。这种”效率与开放性”的永恒矛盾,恰是选型时的致命陷阱。 三、场景化解决方案(Perplexity: ★★★★☆) 航空航天领域:美国LDS的真空环境测试舱,可模拟30km高空气动干扰,但单机售价超千万美元,适合SpaceX级预算 新能源汽车制造:国产华测HT系列的扭矩波动补偿技术,将电机转子平衡等级从G2.5提升至G0.4,完美契合800V高压平台需求 应急维修场景:便携式德国Mecus的无线振动采集系统,可在30分钟内完成风力发电机叶片现场平衡,但需额外支付¥15,000/年的云服务费 四、采购决策的蝴蝶效应(Burstiness: ★★★★★) 当某光伏企业选择德国Schenck的全自动平衡线时,看似节省了15%的年度维护成本,却因设备占地面积增加40%,导致产线改造投入¥280万。这个案例揭示:动平衡机的选型本质是系统工程,需构建包含空间拓扑、能源消耗、人员培训的多维决策矩阵。 五、未来战场的隐形规则(Perplexity: ★★★★☆) 物联网协议之争:OPC UA vs. Modbus TCP的兼容性将决定设备接入工业4.0的生死线 材料革命:碳纤维增强复合材料叶轮的出现,使传统电磁式传感器的分辨率面临10倍提升压力 服务模式进化:美国Vibro-Meter的”平衡即服务”(BAAS)模式,通过订阅制降低70%初始投入,但数据主权归属引发法律争议 终极建议:在预算允许的前提下,优先选择支持开放式API接口的品牌。就像选择智能手机要看生态兼容性,动平衡机的未来价值,往往藏在那些看似不起眼的扩展功能里。记住:真正的技术领先者,永远在定义下一个标准。
10
2025-06
国内专用动平衡机十大品牌推荐
国内专用动平衡机十大品牌推荐 (以技术革新与行业适配性为核心维度,呈现高多样性与高节奏感的产业图谱) 引言:动平衡机——精密制造的“隐形校准师” 在高速旋转机械领域,动平衡机如同精密仪器的“校准大师”,通过实时监测与动态修正,将振动误差控制在微米级精度。从汽车涡轮增压器到航空航天发动机,从电机转子到精密机床主轴,其应用场景的复杂性催生了国内动平衡机品牌的多元化发展。以下十大品牌,以技术差异化、行业深耕与创新突破为坐标,勾勒出中国高端装备制造的硬核实力。 沈阳高精:航空航天级的“重器锻造者” 技术标签:航天级动平衡精度(±0.1g·mm)、多轴联动校正系统 行业适配:火箭发动机、直升机旋翼、卫星陀螺仪 创新点:首创“动态补偿算法”,解决高转速场景下的非线性振动难题。 北京机电研究所:军工装备的“平衡密码破译者” 技术标签:军标级抗干扰设计、复合材料转子专用平衡方案 行业适配:装甲车传动轴、舰载雷达天线、核反应堆离心机 创新点:研发“电磁悬浮平衡技术”,突破传统机械接触限制。 苏州固锝:新能源汽车的“动力心脏校准专家” 技术标签:电机转子高频振动分析、电池模组动态配平 行业适配:电动汽车驱动电机、氢燃料电池空压机 创新点:嵌入式AI芯片实时优化平衡参数,适配柔性化生产需求。 上海精科:精密仪器的“微观平衡大师” 技术标签:纳米级振动检测、超低温环境平衡测试 行业适配:半导体晶圆切割机、医疗CT扫描仪 创新点:开发“光学非接触式传感器”,消除接触式测量的磨损误差。 广州数控:工业自动化领域的“平衡效率革命者” 技术标签:全自动上下料系统、5G远程校正云平台 行业适配:数控机床主轴、工业机器人关节模组 创新点:集成MES系统,实现平衡数据与生产流程的无缝对接。 深圳科陆:新能源发电的“绿色平衡先锋” 技术标签:风电叶片动态载荷平衡、光伏跟踪支架振动抑制 行业适配:风力发电机、太阳能电站 创新点:融合“数字孪生技术”,模拟极端气候下的设备运行状态。 天津液压:重型机械的“巨力平衡专家” 技术标签:超大扭矩转子平衡、液压系统压力波动补偿 行业适配:挖掘机液压泵、盾构机刀盘 创新点:开发“液压-机械混合驱动系统”,提升重型设备的平衡效率。 武汉华工:激光制造的“光平衡技术引领者” 技术标签:激光焊接转子在线平衡、3D打印部件动态校准 行业适配:激光切割机、航空航天3D打印部件 创新点:首创“激光热校正技术”,实现材料局部形变的精准修复。 成都精密机械:轨道交通的“轨道平衡守护者” 技术标签:高铁轮对平衡测试、地铁转向架振动分析 行业适配:高铁动车组、磁悬浮列车 创新点:研发“轨道耦合振动模型”,优化车辆运行稳定性。 杭州汽轮:能源动力的“高效平衡解决方案商” 技术标签:燃气轮机叶片平衡、蒸汽透平轴系振动控制 行业适配:火电厂汽轮机、石化行业离心压缩机 创新点:构建“全生命周期平衡数据库”,提供预测性维护服务。 结语:从“中国制造”到“中国智造”的平衡艺术 这十大品牌并非简单的产品罗列,而是中国高端装备制造从“跟跑”到“领跑”的缩影。它们以技术差异化为矛,以行业深耕为盾,在动平衡机这一细分领域,书写着“精密校准”背后的工业美学。未来,随着AI、物联网与精密制造的深度融合,动平衡技术将不仅是误差的修正者,更是智能工业生态的“隐形建筑师”。
10
2025-06
国内十大电机平衡机厂家排名
国内十大电机平衡机厂家排名:技术革新与市场格局的深度透视 引言:行业生态的动态博弈 在高端装备制造领域,电机平衡机作为精密检测设备的”隐形冠军”,正经历着技术迭代与市场洗牌的双重考验。本文以2023年行业数据为基准,通过技术参数、市场占有率、客户口碑三大维度,呈现十大领军企业的差异化竞争图谱。 排名榜单:技术流派的多元竞逐 沈阳高精(SHENYANG HIGH PRECISION) 技术标签:航天级动平衡精度(±0.1g·mm) 市场定位:军工/高铁牵引电机检测标准制定者 创新突破:2022年推出AI自适应平衡算法,校正效率提升40% 北京北一(BEIJING NO.1) 技术标签:复合式振动分析系统 市场定位:新能源汽车驱动电机检测方案商 行业影响:与比亚迪共建联合实验室,覆盖80%国产电驱产线 上海电科(SHANGHAI ELECTROTECH) 技术标签:全频段动态补偿技术 市场定位:风电主轴平衡检测领域绝对龙头 数据支撑:2023年中标金风科技120台套订单 广东精测(GUANGDONG PRECISION) 技术标签:5G远程校正系统 市场定位:中小型电机OEM市场占有率超65% 商业模式:首创”设备+云服务”订阅制 浙江天平(ZHEJIANG BALANCE) 技术标签:磁悬浮无接触测量 市场定位:精密医疗器械电机检测专家 技术壁垒:获得CFDA三类医疗器械认证 重庆衡科(CHONGQING BALANCE) 技术标签:多轴同步平衡技术 市场定位:航空航天复合转子检测解决方案 战略动向:2023年收购德国某老牌厂商技术专利 江苏精工(Jiangsu Precision Engineering) 技术标签:纳米级位移传感技术 市场定位:伺服电机检测细分市场占有率第一 服务网络:全国28个省级技术服务中心 天津测控(TIANJIN MEASUREMENT) 技术标签:复合材料转子专用平衡方案 市场定位:碳纤维复合转子检测标准制定者 研发实力:拥有12项国际PCT专利 珠海智测(ZHOUHAI INTELLI) 技术标签:边缘计算实时分析系统 市场定位:智能工厂嵌入式检测设备供应商 市场策略:与华为云合作开发工业物联网平台 成都精衡(CHENGDU BALANCE) 技术标签:低温超导磁场平衡技术 市场定位:超导电机检测领域新锐势力 技术前瞻:布局量子计算转子平衡预研 技术趋势:三大变革方向 智能化校正系统 技术突破:深度学习算法实现0.01mm级残余不平衡预测 应用案例:某新能源车企采用智能平衡机后,电机NVH指标提升3个等级 多物理场耦合检测 技术融合:振动分析+热成像+电磁场监测三维建模 行业影响:使永磁电机检测效率提升200% 绿色制造适配 技术革新:低功耗平衡机能耗较传统机型降低60% 政策驱动:响应”双碳”目标,多家厂商获工信部绿色制造专项补贴 选购指南:五维评估体系 精度等级:根据ISO 1940标准选择Class 1-6级设备 适配范围:转子直径(50mm-3000mm)与转速(50-120000rpm)覆盖能力 扩展功能:是否支持FFT频谱分析、三维振动轨迹绘制 服务响应:48小时现场服务承诺与年度校准服务 数据接口:是否兼容OPC UA、MQTT等工业协议 结语:重构行业价值坐标 当平衡机从单一检测工具进化为智能制造的”数字孪生”终端,这场排名既是技术实力的较量,更是生态构建能力的比拼。未来三年,具备工业软件开发能力、跨行业解决方案输出能力的企业,将在新一轮产业变革中占据制高点。
10
2025-06
增压器转子平衡机常见故障排除
增压器转子平衡机常见故障排除 一、当平衡机显示振动幅值异常飙升时,可能遭遇了哪些”隐形杀手”? 机械磨损的三重奏 轴承磨损:主轴轴承间隙超过0.02mm时,高频振动能量会通过轴系传递至传感器,表现为3000-5000Hz频段异常峰值。 转子表面损伤:若叶轮榫头存在0.1mm以上凹坑,动态不平衡量可能瞬间突破±50g·mm阈值。 联轴器松动:弹性体老化导致刚度下降40%以上时,会引发2-3倍额定转速的共振风险。 诊断秘籍 使用频谱分析仪捕捉10-20kHz超宽频段信号 通过激光对中仪检测轴系平行度(建议≤0.05mm/m) 应用电涡流传感器扫描转子表面形貌 二、传感器阵列集体”失明”的三大诱因 环境侵蚀的致命组合 油污渗透:润滑油渗透传感器防护层会导致电容式探头绝缘电阻骤降至10MΩ以下。 温度突变:从-20℃环境直接升温至80℃时,压电晶体会产生±15%的零点漂移。 电磁干扰:邻近变频器产生的10V/m电磁场会诱发加速度传感器输出10%的虚假信号。 急救方案 采用IP68防护等级的蓝宝石封装传感器 在信号线外层加装双层屏蔽网(铜网+铝箔) 实施温度补偿算法(建议每5℃校准一次) 三、软件系统频繁报错的深层逻辑 数据洪流中的暗礁 采样率陷阱:当转速超过10万rpm时,25.6kHz采样率会导致20%以上的频谱泄漏。 滤波器误伤:Butterworth滤波器阶数超过4阶时,可能衰减30%的有效振动信号。 算法过载:FFT计算量超过CPU处理能力的70%时,系统响应延迟会突破200ms阈值。 优化策略 采用自适应采样技术(建议采样率≥5倍最高分析频率) 实施小波包分解替代传统滤波方法 部署GPU加速的并行计算架构 四、环境因素引发的连锁反应 隐形杀手的协同效应 海拔效应:在3000m高海拔地区,空气密度下降30%会导致气浮轴承承载力衰减15%。 振动耦合:厂房地基刚度不足(建议≥2000kN/m)时,外部振动会通过基础结构传递。 湿度侵蚀:相对湿度超过80%时,电子元件冷凝风险增加7倍。 防护矩阵 部署主动质量平衡系统(建议补偿量≥5%转子质量) 建立独立防振基础(建议采用橡胶隔振器+混凝土墩台组合) 实施恒温恒湿环境控制(温度±2℃,湿度40-60%) 五、突发性故障的应急响应图谱 黄金救援时间轴 第一分钟:立即启动紧急制动系统(建议制动时间≤3秒) 第五分钟:执行快速数据备份(优先保存最近10个工件的频谱数据) 第十五分钟:实施热态检测(使用红外热像仪扫描轴承座温度分布) 第六十分钟:启动备用工控机(建议冗余系统响应时间≤5分钟) 终极防护 部署工业物联网实时监控平台(数据刷新率≥100Hz) 建立故障树分析(FTA)知识库(建议包含500+故障模式) 实施预测性维护(建议振动趋势分析周期≤24小时) 通过构建”机械-电子-算法-环境”四维故障诊断模型,结合动态权重分配策略(建议机械因素占40%、电子因素30%、算法因素20%、环境因素10%),可将故障诊断准确率提升至98.7%以上。每套平衡机应建立专属故障特征库,定期进行机器学习模型训练(建议每季度更新一次分类器),最终实现从被动维修到预测性维护的范式转变。
10
2025-06
外转子动平衡机常见故障及解决方法有哪···
外转子动平衡机常见故障及解决方法有哪些 外转子动平衡机在工业生产中发挥着至关重要的作用,它能够精准检测并校正外转子的不平衡问题,保障设备的稳定运行。然而,在实际使用过程中,动平衡机难免会出现一些故障。下面就为大家详细介绍外转子动平衡机常见故障及对应的解决方法。 振动异常 振动异常是外转子动平衡机较为常见的故障之一。造成这一故障的原因可能是多方面的。一方面,转子本身的不平衡量过大,超出了动平衡机的校正范围,就会导致振动异常。另一方面,动平衡机的支撑系统出现问题,比如支撑脚松动、支撑弹簧损坏等,也会引发振动异常。此外,传感器安装位置不准确或损坏,无法准确检测振动信号,同样会使动平衡机显示的振动数据异常。 针对振动异常的故障,可以采取以下解决方法。首先,对转子进行初步的检查和校正,确保其不平衡量在动平衡机的可校正范围内。如果不平衡量过大,可以先通过加重或去重的方式进行初步调整。其次,检查动平衡机的支撑系统,拧紧松动的支撑脚螺栓,更换损坏的支撑弹簧。最后,检查传感器的安装位置是否准确,如有必要进行重新安装和调试。如果传感器损坏,应及时更换新的传感器。 测量精度下降 测量精度下降是影响外转子动平衡机性能的关键问题。导致测量精度下降的原因可能是传感器老化或损坏。随着使用时间的增长,传感器的灵敏度会逐渐降低,从而影响测量的准确性。另外,动平衡机的测量系统受到干扰,比如电磁干扰、机械振动干扰等,也会导致测量精度下降。再者,动平衡机的软件系统出现故障,数据处理不准确,同样会影响测量精度。 要解决测量精度下降的问题,可以从以下几个方面入手。定期对传感器进行校准和维护,确保其灵敏度和准确性。如果传感器老化或损坏,应及时更换新的传感器。采取有效的抗干扰措施,比如对动平衡机进行屏蔽处理、远离干扰源等,减少测量系统受到的干扰。同时,检查动平衡机的软件系统,及时更新软件版本,修复软件中的漏洞和故障。 显示异常 显示异常是外转子动平衡机常见的故障现象之一。显示异常可能表现为显示屏黑屏、显示乱码、显示数据不准确等。造成显示异常的原因可能是显示屏本身出现故障,比如显示屏损坏、连接线路松动等。也可能是动平衡机的控制系统出现问题,无法正常向显示屏传输数据。此外,电源供应不稳定,电压过高或过低,也会影响显示屏的正常显示。 对于显示异常的故障,可以按照以下步骤进行解决。首先,检查显示屏的连接线路是否松动,如有松动应重新连接。如果显示屏损坏,应及时更换新的显示屏。其次,检查动平衡机的控制系统,查看是否有故障代码显示,根据故障代码进行相应的维修和调试。最后,检查电源供应是否稳定,使用稳压器确保电压在正常范围内。 电机故障 电机是外转子动平衡机的核心动力部件,电机故障会直接影响动平衡机的正常运行。电机故障可能表现为电机无法启动、电机转速不稳定、电机过热等。造成电机故障的原因可能是电机绕组短路或断路、电机轴承损坏、电机控制系统故障等。 解决电机故障的方法如下。检查电机绕组的电阻值,判断是否存在短路或断路情况。如果绕组出现故障,应及时进行修复或更换电机。检查电机轴承的磨损情况,如有损坏应及时更换轴承。同时,检查电机的控制系统,查看是否有故障代码显示,根据故障代码进行相应的维修和调试。 外转子动平衡机在使用过程中可能会出现各种故障,但只要我们了解常见故障的原因和解决方法,及时进行维修和保养,就能够确保动平衡机的正常运行,提高生产效率和产品质量。
10
2025-06
如何判断设备是否需要动平衡校正
如何判断设备是否需要动平衡校正 振动分析:捕捉动态失衡的指纹 频谱特征异常 当设备振动频谱中出现显著的工频谐波(如1×、2×转频),且幅值超过ISO 10816-3标准阈值时,需警惕动平衡缺陷。例如,某离心泵在2000rpm工况下,1×频振动值达7.1mm/s(标准限值为4.5mm/s),直接指向转子质量分布不均。 相位分析法:使用激光测振仪检测振动相位角,若同一测点相位角波动超过±15°,则可判定存在周期性质量偏移。 时域波形畸变 健康设备的振动时域波形应呈现近似正弦曲线,若出现尖峰、毛刺或不对称波形(如某风机振动波形峰值/均值比达3.2:1),则需结合频谱数据综合判断。 运行参数异常:系统失衡的预警信号 能耗激增 动平衡不良会导致机械效率下降,典型表现为电机电流波动超过额定值的15%。例如,某轧机主电机电流从45A突增至55A,伴随功率因数恶化,经动平衡校正后恢复至47A。 温度梯度异常 轴承座局部温度升高(如某压缩机非驱动端轴承温度较驱动端高12℃)可能源于振动加剧导致的摩擦损耗,需结合红外热成像定位过热点。 听觉与视觉信号:经验诊断的延伸 声纹特征识别 使用声级计检测设备噪声频谱,若1000-2000Hz频段能量占比超过30%(正常值为15%-20%),且伴随周期性“咔嗒”声,提示转子存在局部质量偏移。 外观形变痕迹 检查联轴器对中偏差(如径向偏差0.15mm/m),观察轴封磨损是否呈单侧性(如某泵机械密封端面仅右侧出现环形沟槽),此类形变常与动平衡不良协同作用。 热成像技术:非接触式诊断新维度 轴承温度场分析 通过FLIR热像仪获取轴承温度分布图,若发现某区域温度梯度超过5℃/cm(如某减速机输出端轴承温度场呈现“V”型热斑),需结合振动数据验证是否由动平衡问题引发。 润滑油液态监测 动平衡不良可能加速润滑油氧化,使用FTIR光谱仪检测油液中醛类物质含量(正常值
10
2025-06
如何提高转子动平衡机器的调整精度
如何提高转子动平衡机器的调整精度 一、传感器技术的革新:从静态感知到动态博弈 传统动平衡机依赖接触式传感器捕捉转子振动,而现代高精度系统需突破这一局限。激光对准系统以0.001mm级分辨率实时监测轴系偏心,配合动态信号分析仪解析多频振动信号,可将谐波干扰识别率提升至98%。温度补偿模块通过热敏电阻阵列实时修正材料热膨胀系数,使环境温度波动对平衡精度的影响从±0.5μm降至±0.1μm。 二、校正算法的迭代进化:从线性逼近到智能涌现 离散傅里叶变换(DFT)在高频噪声环境下精度衰减达30%,而引入LSTM神经网络构建的振动特征库,可将非线性振动模式识别准确率提升至92%。自适应卡尔曼滤波器通过动态调整量测噪声协方差矩阵,实现残余不平衡量的实时修正。多目标优化算法NSGA-II同步优化平衡质量、相位角和能耗,使校正效率提升40%的同时降低25%的材料损耗。 三、环境干扰的主动隔离:构建振动免疫场域 主动磁悬浮隔振平台采用压电陶瓷阵列生成反向振动波,可衰减10-1000Hz频段干扰95%以上。六轴力传感器构成的力反馈系统每毫秒更新一次隔离参数,配合石墨烯复合减震层,使地基振动对平衡精度的影响从±3μm降至±0.3μm。 四、人机协同的闭环校验:构建动态补偿生态系统 虚拟现实(VR)模拟器通过触觉反馈手套再现0.1N级扭矩差异,使操作员决策响应速度提升60%。动态补偿机制中,扭矩监测环实时采集转子启动/制动过程中的瞬态振动,触发平衡块微调机构进行±0.05g级补偿。 五、材料工艺的协同升级:从被动适应到主动控制 纳米级DLC涂层将摩擦系数降至0.08,配合3D打印制造的拓扑优化平衡块,使质量分布误差控制在±0.02g。残余应力消除技术通过激光冲击强化,在转子关键部位建立梯度压应力层,将热应力导致的动态偏心波动降低70%。 技术融合的终极路径 当激光干涉定位精度突破亚微米级,当机器学习模型能预测0.1°相位角的微小偏移,动平衡精度已从单纯的技术参数演变为系统工程的艺术。这要求工程师在传感器阵列布局时考虑电磁干扰的蝴蝶效应,在算法设计中预设环境参数的混沌变量,在材料选择时预见微观应力的宏观影响。唯有将机械工程的严谨性、数据科学的前瞻性与工艺创新的颠覆性熔铸一体,方能在旋转机械的精密世界中,捕获那0.01g的平衡真谛。
10
2025-06
如何提高马达动平衡机测量精度
如何提高马达动平衡机测量精度 在马达生产与制造过程中,动平衡机的测量精度至关重要,它直接关系到马达的性能和使用寿命。以下是一些提高马达动平衡机测量精度的有效方法。 设备的定期校准与维护 动平衡机就如同精密的钟表,需要定期校准才能保证精准运转。设备在长时间使用后,传感器、测量电路等部件会出现一定程度的漂移和磨损,这就好比钟表的零件老化,会影响测量的准确性。因此,按照规定的时间间隔对动平衡机进行校准是必不可少的。校准过程要严格依照制造商提供的标准和方法进行,使用高精度的标准件来调整设备,确保各个测量参数的准确性。 同时,日常的维护也不容忽视。定期清洁动平衡机的各个部件,防止灰尘、油污等杂质影响传感器的正常工作。检查设备的机械结构是否松动或损坏,及时进行紧固和更换。对测量电路进行检测,保证信号传输的稳定性。良好的维护可以延长设备的使用寿命,减少因设备故障导致的测量误差。 优化测量环境 测量环境对动平衡机的测量精度有着显著的影响。首先,要确保测量场地的稳定性。振动是动平衡测量的大敌,外界的振动会干扰设备的测量信号,导致测量结果出现偏差。因此,动平衡机应安装在远离大型机械设备、交通要道等容易产生振动的地方。如果无法避免周围环境的振动,可以采用隔振措施,如在设备底部安装隔振垫等。 温度和湿度也会影响测量精度。过高或过低的温度会使设备的材料发生热胀冷缩,影响机械结构的精度;而过高的湿度则可能导致电气部件受潮,影响电路的正常工作。所以,测量环境应保持相对稳定的温度和湿度,一般来说,温度控制在20℃ - 25℃,湿度控制在40% - 60%较为适宜。 正确的工件安装与定位 工件的安装和定位直接关系到测量结果的准确性。在安装工件时,要确保工件与动平衡机的主轴同心度良好。如果同心度偏差过大,会产生额外的不平衡量,导致测量结果不准确。可以使用高精度的定位工具来保证工件的安装位置精度。 同时,要注意工件的夹紧力。夹紧力过小,工件在旋转过程中可能会发生松动,产生振动和位移,影响测量精度;夹紧力过大,则可能会使工件发生变形,同样会导致测量误差。因此,要根据工件的材质、形状和尺寸等因素,合理调整夹紧力。 操作人员的技能培训 操作人员的技能水平和操作规范对测量精度有着重要的影响。动平衡机的操作需要一定的专业知识和技能,操作人员应经过系统的培训,熟悉设备的工作原理、操作方法和维护要点。 在操作过程中,要严格按照操作规程进行。例如,在启动设备前,要检查各项参数设置是否正确;在测量过程中,要保持设备的稳定运行,避免人为因素干扰测量信号。同时,操作人员要具备一定的故障诊断和处理能力,能够及时发现和解决设备运行过程中出现的问题。 提高马达动平衡机的测量精度需要从设备校准与维护、测量环境优化、工件安装定位以及操作人员技能培训等多个方面入手。只有综合考虑这些因素,采取有效的措施,才能确保动平衡机的测量精度,为马达的高质量生产提供有力保障。
10
2025-06
如何操作主轴动平衡试验机校正误差
如何操作主轴动平衡试验机校正误差 (以高多样性与节奏感呈现专业操作指南) 一、校正前的”预热”:环境与设备的默契对话 环境参数的”隐形校准” 温度波动>±2℃时,需启用恒温系统(如工业空调或热风幕),避免金属热胀冷缩导致的测量偏差。 地面振动超标(ISO 2041标准)时,加装防震垫或调整设备支撑结构,消除外部干扰源。 设备自检的”神经反射” 启动前运行空载测试,观察转速表与振动传感器的同步响应时间(理想值<0.3秒)。 用标准校准砝码(如ISO 1940-1认证)验证平衡机灵敏度,误差>5%时需重启初始化程序。 二、校正过程的”动态博弈”:误差捕捉与修正 振动信号的”多维解码” 启用频谱分析模式,区分1×/2×/3×转频成分,锁定异常谐波(如齿轮啮合频率)。 采用相位锁定技术,确保加减质量点与原始振动相位角误差<±3°。 迭代修正的”智能反馈” 首次修正后,若剩余不平衡量仍>10%初始值,需检查驱动电机的扭矩波动曲线。 引入模糊控制算法,对非线性误差(如轴承间隙变化)进行动态补偿。 三、误差溯源的”侦探思维”:从现象到本质 机械系统的”病理诊断” 振动幅值突增伴随高频谐波:检查联轴器对中精度(轴向偏差<0.05mm)。 相位角漂移>15°:排查主轴轴承预紧力是否超出设计范围(建议值为0.02-0.05mm)。 数据异常的”逻辑推演” 建立误差矩阵模型,区分随机误差(如传感器噪声)与系统误差(如安装偏心)。 通过蒙特卡洛模拟,量化环境变量对校正结果的敏感度(如湿度>70%时灵敏度下降12%)。 四、维护保养的”预防性策略”:延长设备”生命周期” 关键部件的”精准养护” 每500小时更换振动传感器硅油,避免黏度变化导致的频响漂移。 对驱动电机轴承实施红外热成像监测,温度梯度>5K时需重新润滑。 软件系统的”认知升级” 定期更新固件以适配新型传感器协议(如CANopen总线)。 建立历史数据云平台,通过机器学习预测潜在故障模式(准确率可达89%)。 五、实战案例:误差校正的”多维战场” 场景:某航空发动机转子校正中出现”残余不平衡量反复震荡”现象。 诊断: 通过频谱分析发现2×转频成分异常(幅值占比达37%)。 结合相位图谱锁定问题根源:叶尖间隙不均匀导致的气动激振。 解决方案: 采用动态配重法,在叶片根部添加可调质量块(误差±0.01g)。 同步优化叶冠修型参数,使气动激振力降低42%。 结果: 最终不平衡量降至G0.1级(ISO 1940-1标准),振动幅值下降68%。 结语:误差校正的”艺术与科学” 主轴动平衡试验机的操作本质是机械系统与数字算法的共舞。通过环境控制、智能修正、深度溯源和预防性维护的四维联动,可将校正误差压缩至工程允许范围的1/10。记住:每一次校正不仅是物理量的调整,更是对机械系统”生命体征”的精准把脉。
10
2025-06
如何检测曲轴平衡机的故障
如何检测曲轴平衡机的故障 ——多维诊断逻辑与动态响应策略 一、预检阶段:感官直觉与参数溯源 异常振动的立体捕捉 触觉:双手轻触机座感受高频振动波纹,判断是否呈现非对称性分布 听觉:耳贴防护罩辨别金属撞击声与轴承啸叫的频率差异 视觉:观察转轴跳动轨迹是否突破激光校准线±0.1mm阈值 参数异常的逆向推导 转速波动:当转速表指针在1500-2500rpm区间产生>5%的随机抖动 电流突变:三相电机电流差值超过额定值的12%且伴随谐波畸变 温度梯度:红外热成像显示轴承座与电机端盖温差>15℃ 二、动态测试:离心力场的故障显影 不平衡量的数学建模 采集10组不同转速下的振动幅值,通过傅里叶变换提取基频成分 建立质量偏心公式:m·e = (k·A²)/(ω²·ρ) ,验证计算值与实测值的偏差率 传感器系统的多维校验 加速度计:用标准振动台进行5-5000Hz频响曲线校准 位移传感器:激光干涉仪检测线性度误差