Copyright © 2003-2019 上海申岢动平衡机制造有限公司, All Rights Reserved 沪ICP备16012006号-5 友情链接:
上海动平衡机
搜索


动平衡机加工与生产线其他工序的衔接优化策略
- 分类:行业新闻
- 作者:申岢编辑部
- 来源:上海申岢动平衡机制造有限公司
- 发布时间:2025-04-21
- 访问量:81
动平衡机加工与生产线其他工序的衔接优化是提升整体生产效率、减少瓶颈的关键环节。以下是一套系统性优化策略,涵盖技术、流程和管理三个维度:
1. 生产节拍同步化
- 瓶颈分析:通过时间观测或仿真工具(如FlexSim)识别动平衡工序是否成为瓶颈。若其周期时间(Cycle Time)长于其他工序,需优先优化。
- 动态缓冲设计:
- 在动平衡机前后设置智能缓存区(如FIFO队列或自动化料仓),平衡上下游节拍差异。
- 应用ANDON系统实时监控缓存状态,触发预警机制。
- 并行化改进:针对高耗时动平衡工艺,采用多工位并行加工(如双头动平衡机)或模块化工作站。
2. 数据流与工艺集成
- 数字化孪生:构建动平衡机的数字模型,与MES/ERP系统集成,实现参数(如转速、修正量)自动下发和结果实时回传。
- 闭环反馈控制:
- 前道工序(如车削/铣削)根据动平衡结果动态调整加工参数(如预留修正余量)。
- 后道工序(如装配)基于动平衡数据匹配公差兼容件,减少二次返工。
- AI预测优化:利用历史数据训练机器学习模型,预测动平衡修正量并提前生成补偿方案。
3. 物理布局与物流优化
- 单元化布局:将动平衡机与关联工序(如去重/增重修正、检测)整合为独立制造单元(Cell),减少物料搬运。
- 自动化物流衔接:
- 采用AGV/RGV实现工件自动转运,通过RFID/二维码识别工件信息并匹配加工参数。
- 在高速生产线中引入机械臂或桁架机器人完成上下料,消除人工干预延迟。
- 人机协作设计:优化操作界面(HMI)和工装夹具,缩短换型时间(SMED方法)。
4. 质量管控与异常处理
- 在线检测集成:在动平衡机后设置光谱分析或视觉检测,同步完成动平衡与表面质量检验。
- 异常分流机制:
- 不合格品通过分支滑道自动进入返修线,避免阻塞主生产线。
- 应用SPC(统计过程控制)监控动平衡过程稳定性,触发自动停机或参数校准。
- 根因分析(RCA):建立跨工序质量问题追溯系统,快速定位动平衡异常源头(如毛坯质量、前序加工误差)。
5. 柔性化与可扩展性
- 模块化设备选型:选用支持快速换型(如气动夹具、参数预设)的动平衡机,适应多品种生产。
- 动态调度算法:在混线生产中,通过APS(高级计划排程)系统动态分配动平衡机资源,优先处理关键路径工件。
- 预留升级接口:在设备选型时兼容未来技术扩展(如5G通信、边缘计算),降低后续改造难度。
6. 人员协同与培训
- 跨工序培训:培养操作人员掌握前后工序基础知识(如动平衡结果对装配的影响),促进主动协同。
- 标准化作业(SOP):制定动平衡机与上下游联动的标准操作流程,明确异常处理责任链。
- 绩效联动考核:将动平衡工序效率与前后工序团队KPI绑定,避免局部优化损害全局效率。
7. 能效与可持续性优化
- 能源监控:安装智能电表监测动平衡机能耗,与生产节拍联动实现待机节能。
- 绿色工艺改进:采用激光修正替代传统钻孔去重,减少金属废料并提升精度。
- 预测性维护:通过振动传感器和温度监测预判动平衡机故障,利用生产间隙完成维护。
实施路径建议
- 现状诊断:通过VSM(价值流图)分析现有流程,量化动平衡工序的衔接损失。
- 试点验证:选择典型产品线进行局部优化(如数据接口升级+AGV导入),验证ROI。
- 规模化推广:基于试点经验制定标准化优化模板,复制到其他产线。
- 持续改进:建立动态评估机制,定期迭代优化策略。
通过上述策略,企业可将动平衡工序深度融入生产线,实现从“孤立加工点”到“智能协同节点”的转型,最终达成生产效率提升15%-30%、质量损失降低20%以上的典型收益。
下一个:
动平衡机加工与数字孪生技术的结合前景
下一个:
动平衡机加工与数字孪生技术的结合前景
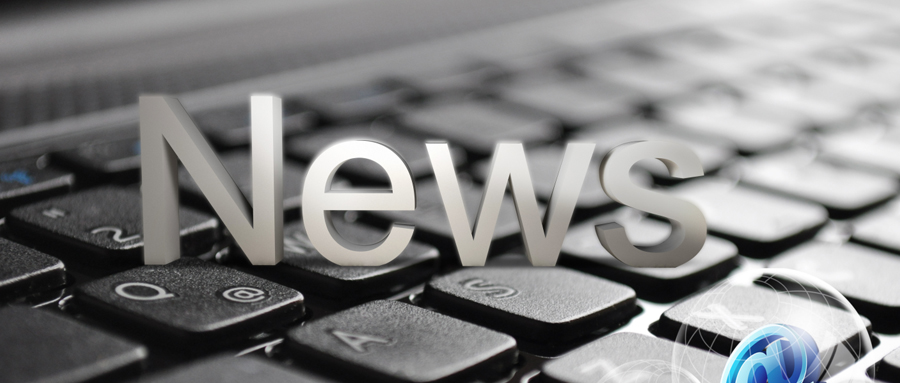