Copyright © 2003-2019 上海申岢动平衡机制造有限公司, All Rights Reserved 沪ICP备16012006号-5 友情链接:
上海动平衡机
搜索


动平衡机加工时不同工件直径对测量结果的影响分析
- 分类:行业新闻
- 作者:申岢编辑部
- 来源:上海申岢动平衡机制造有限公司
- 发布时间:2025-04-21
- 访问量:82
在动平衡加工过程中,工件直径的变化会显著影响测量结果的准确性,需从多个角度分析其影响机制并提出应对措施。以下是详细的分析与建议:
1. 转动惯量与离心力的影响
- 影响机制:
- 转动惯量公式为 ( J = mr^2 ),直径(半径 ( r ))增大会显著增加转动惯量,导致相同转速下的离心力 ( F = mromega^2 ) 增大。
- 传感器可能因过载而失真,或小直径工件信号过弱,导致测量灵敏度下降。
- 应对措施:
- 根据工件直径调整动平衡机的量程范围,确保传感器信号在有效区间内。
- 对大直径工件适当降低转速,小直径工件提高转速,以优化信噪比。
2. 转速选择的适配性
- 影响机制:
- 大直径工件需降低转速以避免离心力超限,但转速过低可能导致不平衡信号无法有效激发;小直径工件需较高转速以提高检测灵敏度。
- 应对措施:
- 根据直径计算临界转速,选择最佳平衡转速范围(通常为工作转速的80%)。
- 使用变频器动态调整转速,适配不同直径工件的需求。
3. 支撑系统的匹配性
- 影响机制:
- 直径变化可能改变工件的重心位置和重量分布,导致支撑轮或夹具受力不均,引入额外振动。
- 应对措施:
- 调整支撑轮间距,确保工件旋转时轴线稳定。
- 定制适配不同直径的夹具,如V型块或膨胀芯轴,减少装夹误差。
4. 相位角检测精度
- 影响机制:
- 直径增大时,相同相位角误差对应的线速度偏差更大,导致不平衡位置识别误差。
- 应对措施:
- 提高转速采样频率,确保相位触发信号与工件标记同步。
- 使用激光或光学传感器辅助定位,提升相位角检测精度。
5. 校准与参数输入的准确性
- 影响机制:
- 动平衡机的算法依赖输入的直径、重量等参数。直径输入错误会导致离心力计算偏差。
- 应对措施:
- 严格校准设备,每次更换工件时重新输入直径、质量等参数。
- 采用自动测量系统(如激光扫描)实时获取工件几何数据。
6. 材料分布与结构差异
- 影响机制:
- 大直径工件可能为中空结构(如风机叶轮),质量分布靠近边缘,放大不平衡效应。
- 应对措施:
- 对异形工件进行有限元分析(FEA),预判不平衡区域。
- 采用分段平衡法,先粗平衡再精平衡,减少直径带来的分布误差。
7. 设备选型与调整
- 应用建议:
- 立式动平衡机:适合大直径短轴工件(如齿轮、飞轮)。
- 卧式动平衡机:适合长径比大的工件(如电机转子)。
- 对于超大型工件(直径>2m),选择落地式动平衡机并配备移动传感器。
示例分析
- 直径翻倍的影响:
- 若直径从200mm增至400mm,半径 ( r ) 变为2倍,离心力 ( F ) 增至4倍(( F propto r ))。
- 若不调整转速,传感器可能过载,需将转速降至原值的 ( 1/sqrt{2} )(约70%)以保持离心力恒定。
总结:优化步骤
- 参数校准:严格输入直径、质量、转速等参数。
- 设备适配:根据直径选择机型及支撑方案。
- 动态调整:优化转速与量程,匹配不同直径的测量需求。
- 精度验证:使用标准试重法验证测量结果,确保误差<10%。 通过系统分析直径的影响并针对性调整,可显著提升动平衡加工的精度与效率,减少返工率。
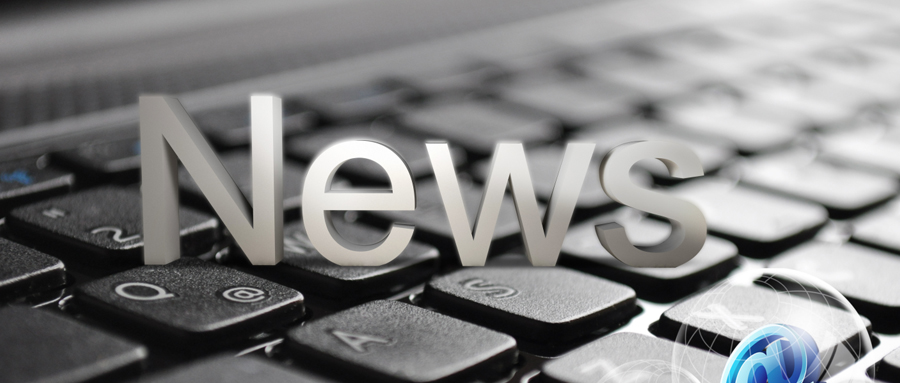