Copyright © 2003-2019 上海申岢动平衡机制造有限公司, All Rights Reserved 沪ICP备16012006号-5 友情链接:
上海动平衡机
搜索


曲棍动平衡机加工后轴承温度异常的原因及处理
- 分类:行业新闻
- 作者:申岢编辑部
- 来源:上海申岢动平衡机制造有限公司
- 发布时间:2025-04-16
- 访问量:78
曲轴动平衡机加工后轴承温度异常是一个常见的设备故障问题,可能由多种原因引起。以下是可能的原因及对应的处理方法,供参考:
一、轴承温度异常的原因
- 润滑不良
- 原因:润滑油/脂不足、变质、型号不匹配,或润滑系统堵塞导致供油不足。
- 表现:轴承摩擦增大,温升明显,可能伴随异响。
- 原因:润滑油/脂不足、变质、型号不匹配,或润滑系统堵塞导致供油不足。
- 轴承安装问题
- 原因:轴承安装时未对中、预紧力过大或过小、轴向/径向间隙调整不当,或轴承座配合过紧(如过盈量过大)。
- 表现:运行时轴承局部过热,振动异常。
- 原因:轴承安装时未对中、预紧力过大或过小、轴向/径向间隙调整不当,或轴承座配合过紧(如过盈量过大)。
- 负载过大
- 原因:动平衡校正时参数设置错误(如转速过高、校正量过大),导致轴承承受额外载荷。
- 表现:设备运行时振动剧烈,温度快速上升。
- 原因:动平衡校正时参数设置错误(如转速过高、校正量过大),导致轴承承受额外载荷。
- 轴承本身损坏
- 原因:轴承滚道磨损、保持架变形、滚动体剥落等内部损伤。
- 表现:温度异常且伴随金属摩擦声或周期性异响。
- 原因:轴承滚道磨损、保持架变形、滚动体剥落等内部损伤。
- 动平衡未校正到位
- 原因:曲轴动平衡未达标,残余不平衡量导致轴承长期受交变应力,加速发热。
- 表现:温度随运行时间逐渐升高,振动幅度大。
- 原因:曲轴动平衡未达标,残余不平衡量导致轴承长期受交变应力,加速发热。
- 冷却系统故障
- 原因:散热风扇故障、冷却液循环不畅(如管路堵塞、泵失效)。
- 表现:温度持续升高,散热部件表面无风感或冷却液流量不足。
- 原因:散热风扇故障、冷却液循环不畅(如管路堵塞、泵失效)。
- 异物污染
- 原因:加工碎屑、粉尘进入轴承内部,或润滑油脂混入杂质。
- 表现:轴承运行卡滞,温度波动异常。
- 原因:加工碎屑、粉尘进入轴承内部,或润滑油脂混入杂质。
- 运行参数不当
- 原因:动平衡机长时间超负荷运行,或启停频率过高导致轴承疲劳。
- 原因:动平衡机长时间超负荷运行,或启停频率过高导致轴承疲劳。
- 设备老化
- 原因:轴承长期使用后磨损、金属疲劳,或密封件老化导致润滑失效。
- 原因:轴承长期使用后磨损、金属疲劳,或密封件老化导致润滑失效。
二、处理方法
- 立即停机检查
- 发现温度异常后,立即停止运行,避免轴承因高温烧毁或引发二次损伤。
- 发现温度异常后,立即停止运行,避免轴承因高温烧毁或引发二次损伤。
- 润滑系统排查
- 检查润滑油量、油质及型号是否符合要求,必要时更换新油/脂。
- 清理润滑管路堵塞点,确保供油畅通。
- 检查润滑油量、油质及型号是否符合要求,必要时更换新油/脂。
- 轴承安装复检
- 重新检查轴承安装精度,确保对中良好、预紧力适中,并调整轴向/径向间隙。
- 使用千分表检测轴承座的同轴度和圆度。
- 重新检查轴承安装精度,确保对中良好、预紧力适中,并调整轴向/径向间隙。
- 动平衡参数校正
- 重新校验曲轴动平衡,确保残余不平衡量在允许范围内。
- 降低试验转速,观察温度是否恢复正常。
- 重新校验曲轴动平衡,确保残余不平衡量在允许范围内。
- 轴承状态检测
- 拆卸轴承,检查滚道、滚动体、保持架是否有损伤。
- 使用听诊器或振动分析仪判断异响来源,必要时更换新轴承。
- 拆卸轴承,检查滚道、滚动体、保持架是否有损伤。
- 冷却系统维护
- 清理散热风扇或冷却液管路,检查泵和阀门是否正常工作。
- 若环境温度过高,可增加外部散热措施。
- 清理散热风扇或冷却液管路,检查泵和阀门是否正常工作。
- 清洁与密封
- 清除轴承座周围碎屑,检查密封圈是否破损,防止污染物进入。
- 清除轴承座周围碎屑,检查密封圈是否破损,防止污染物进入。
- 调整运行参数
- 优化加工参数,避免长时间超负荷运行,合理规划设备启停周期。
- 优化加工参数,避免长时间超负荷运行,合理规划设备启停周期。
- 预防性维护
- 定期更换轴承及润滑剂,建立设备点检制度,记录温度、振动等数据。
- 定期更换轴承及润滑剂,建立设备点检制度,记录温度、振动等数据。
三、预防措施
- 每次开机前检查润滑系统及冷却装置。
- 使用高精度传感器实时监控轴承温度和振动。
- 选择符合设备要求的轴承型号(如高速轴承或重载轴承)。
- 对新安装或维修后的设备进行空载试运行,逐步加载测试。
总结
轴承温度异常往往由多种因素叠加导致,需结合设备运行状态和工艺参数综合分析。快速定位问题并采取针对性措施是关键,同时建议定期维护以延长轴承寿命。若反复出现异常,需联系设备厂家或专业工程师进一步诊断。
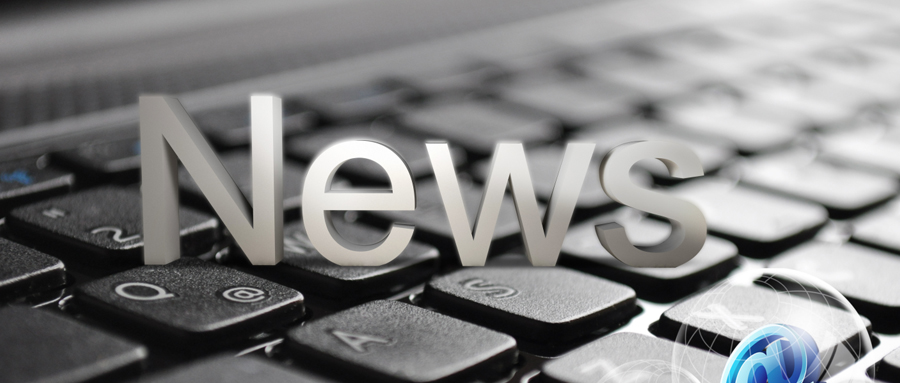