Copyright © 2003-2019 上海申岢动平衡机制造有限公司, All Rights Reserved 沪ICP备16012006号-5 友情链接:
上海动平衡机
搜索


风电叶片动平衡机加工的难点及解决方案
- 分类:行业新闻
- 作者:申岢编辑部
- 来源:上海申岢动平衡机制造有限公司
- 发布时间:2025-04-09
- 访问量:65
风电叶片动平衡加工是风力发电机生产中的关键环节,其难点主要源于叶片尺寸大、结构复杂、材料特殊以及动态精度要求高。以下是具体难点及对应的解决方案:
一、主要难点
- 叶片尺寸大,工装设计复杂
- 叶片长度可达80米以上,加工时需稳定支撑,对工装刚性和定位精度要求极高。
- 叶片形状不规则(气动翼型),导致夹具设计难度大,易因重力或振动产生形变。
- 材料不均匀性影响平衡精度
- 叶片采用玻璃纤维/碳纤维复合材料,密度分布可能存在局部差异(如树脂固化不均、铺层误差)。
- 加工后内部缺陷(如气泡、分层)可能导致质量分布失衡。
- 动态测量精度不足
- 叶片转速低(通常低于30 RPM),传统动平衡机难以捕捉微小振动信号。
- 环境干扰(如车间振动、温度变化)影响传感器数据可靠性。
- 配重工艺效率低
- 传统人工配重依赖经验,需反复测试,耗时长且精度不稳定。
- 叶片表面为曲面,配重块安装位置和方式受限。
- 成本与生产节拍压力
- 大型动平衡设备投资高,维护成本高,中小型企业难以负担。
- 叶片生产批量大,需缩短单件加工时间以满足交付需求。
二、解决方案
- 优化工装与支撑系统
- 采用模块化夹具设计,结合有限元分析(FEA)优化支撑点布局,减少叶片形变。
- 使用液压或气动自适应调平系统,实时补偿重力引起的挠曲变形。
- 高精度材料检测与预处理
- 通过激光扫描和三维测量技术建立叶片质量分布模型,预测潜在失衡区域。
- 在铺层工艺中引入自动化质量监测,减少材料不均匀性。
- 动态平衡技术创新
- 采用高灵敏度光纤传感器或MEMS传感器,搭配抗干扰算法(如小波降噪)提升低速振动信号捕捉能力。
- 在平衡机底座安装主动隔振系统,隔离环境振动干扰。
- 智能化配重工艺
- 基于机器学习算法(如遗传算法)优化配重方案,自动计算最小配重量和最佳位置。
- 开发非侵入式配重技术,如电磁吸附配重块或内部灌注微球调整质量分布。
- 低成本高效生产方案
- 推广模块化动平衡机设计,支持多型号叶片兼容加工,降低设备投入。
- 应用数字孪生技术,通过虚拟调试减少实际加工迭代次数,缩短周期。
- 数据驱动与闭环控制
- 集成物联网(IoT)实时采集加工数据,通过边缘计算实现动态校准。
- 建立叶片动平衡数据库,利用大数据分析优化工艺参数。
三、未来趋势
- 智能化方向:结合AI算法实现自学习平衡策略,减少人工干预。
- 在线动平衡技术:在叶片运行过程中实时监测并调整平衡状态(如通过压电作动器)。
- 轻量化材料创新:开发密度更均匀的复合材料,从根本上降低失衡风险。
通过上述技术手段,可显著提升风电叶片动平衡加工的效率、精度和经济性,助力风电行业向高可靠性、低成本制造方向发展。
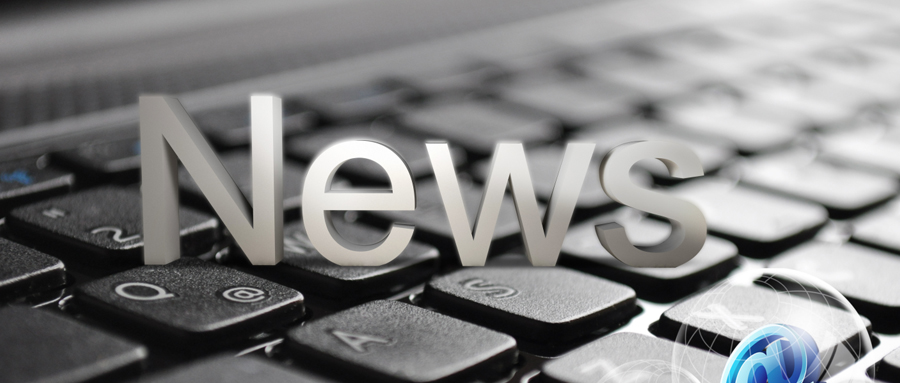