

动平衡校正测试:保障设备稳定运行的核心技术
- 分类:行业新闻
- 作者:申岢编辑部
- 来源:上海申岢动平衡机制造有限公司
- 发布时间:2025-03-25
- 访问量:86
在工业制造、能源发电、航空航天等领域,旋转机械设备的稳定运行直接影响生产效率与安全性。由于材料加工误差、装配偏差或长期磨损,旋转部件往往会产生质量分布不均的问题,进而引发振动、噪声甚至设备损坏。动平衡校正测试正是针对这一问题的关键技术,其通过精准测量与调整,恢复旋转体的动态平衡状态,为设备的长周期平稳运行提供保障。
一、动平衡问题的危害与测试原理
当旋转体的质心偏离旋转中心轴时,会产生周期性离心力,导致设备出现异常振动。这种振动不仅加速轴承、齿轮等零部件的磨损,还可能引发机械共振,造成结构断裂等严重事故。例如,一台转速3000r/min的电机转子,若存在10g·mm的不平衡量,产生的离心力可达约100N,足以导致设备剧烈抖动。 动平衡校正测试的核心原理基于力学平衡理论:通过传感器采集旋转体在运转时的振动信号,结合相位分析技术,精确计算出不平衡量的位置与大小。测试系统通常包含振动传感器、转速测量单元、数据分析模块等,能够实时监测设备振动频谱,定位不平衡质量所在的角位置,并为校正提供量化依据。
二、校正测试的关键实施步骤
设备预检与参数设定
测试前需确认设备基础稳固性,排除轴承损坏、连接松动等干扰因素。根据转子类型(刚性/柔性)选择单平面或双平面校正模式,设定转速范围(通常不低于工作转速的80%)。数据采集与分析
采用非接触式激光测振仪或压电传感器,在X/Y方向同步采集振动幅值与相位数据。通过傅里叶变换将时域信号转化为频域图谱,分离出工频振动分量。智能算法自动计算初始不平衡量,精度可达0.1g·mm/kg。校正方案制定
根据测试结果确定配重位置与质量,常见校正方式包括焊接配重块、钻孔去重或可调节平衡环。对于精密设备,需采用矢量分解法优化多平面配重组合,确保残余不平衡量低于ISO1940标准规定的G6.3级要求。效果验证与优化
校正后需进行复测验证,通过Bode图观察振动幅值衰减情况。对于高速转子(如燃气轮机),还需进行过临界转速测试,验证动态稳定性是否达标。三、技术创新与行业应用
随着检测技术的发展,动平衡校正已从传统离线测试向在线监测升级。激光辅助平衡系统可实现非接触式实时测量,特别适用于高温、高危环境下的设备维护。人工智能算法的引入,使系统能够自主学习设备振动特征,提前预警潜在失衡风险。 在风电领域,针对长达80米的叶片,采用模态平衡技术结合有限元仿真,可将整机振动值降低60%以上。而在微电子制造中,精密主轴动平衡精度要求达到0.01μm级,需借助真空环境下的超高速平衡机完成校正。
四、提升校正效率的实践要点
环境控制:减少测试现场气流扰动与电磁干扰
基准标记:使用高对比度反光贴精准定位相位角
误差补偿:校正夹具质量需计入计算系统
数据管理:建立设备平衡档案,追踪历史变化趋势
结语
动平衡校正测试作为旋转机械健康管理的重要环节,既需要严谨的工程技术手段,也离不开智能化检测体系的支撑。随着工业设备向高速化、精密化发展,动态平衡控制技术将持续迭代,为设备可靠性提升与节能降耗创造更大价值。企业应建立定期检测机制,将动平衡管理纳入预防性维护体系,最大限度降低非计划停机风险。
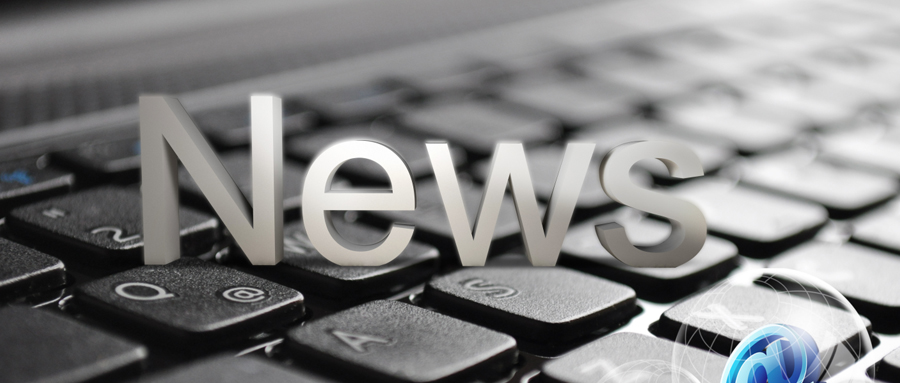