

动平衡测定测试仪:精密制造的无声守护者
- 分类:行业新闻
- 作者:申岢编辑部
- 来源:上海申岢动平衡机制造有限公司
- 发布时间:2025-03-25
- 访问量:80
在现代化工业体系中,机械振动就像潜伏在设备内部的隐形杀手,每年造成数以亿计的经济损失。动平衡测定测试仪作为对抗机械振动的核心武器,正在重塑精密制造的质量标准。这台融合多学科技术的精密仪器,通过数字化的检测手段,为旋转机械构建起动态平衡的防护屏障。
一、技术创新的突破性演进
现代动平衡测定技术突破传统机械补偿的局限,采用多传感器融合检测系统,能够在0.1秒内完成振动信号的实时采集。高灵敏度压电传感器阵列可捕捉到微米级的振幅变化,配合相位补偿算法,将检测精度提升至0.01g·mm的行业新高度。
智能化分析模块集成了深度学习算法,可自动识别转子类型并匹配最优校正方案。当检测到涡轮叶片的不平衡量时,系统能自动生成三维补偿模型,指导操作者精确配重。这种智能诊断能力使调试效率提升300%,彻底改变了传统依赖人工经验的作业模式。
便携式设计突破实验室限制,紧凑型主机重量控制在5kg以内,配备无线传输模块实现移动检测。在风力发电机组现场,技术人员仅需15分钟即可完成叶轮系统的动态平衡检测,相比传统方法节省80%的作业时间。
二、工业应用的革新实践
在航空发动机维修领域,设备能精准识别直径1.2米的涡轮盘存在的细微质量偏差。通过多点位振动谱分析,系统可定位到特定叶片的材料缺陷,为关键零部件的可靠性评估提供量化依据。某型发动机经动态平衡优化后,振动值降低至ISO标准值的1/3。
新能源汽车驱动电机生产线上,在线式动平衡系统构建起零缺陷制造闭环。每分钟处理12个转子的检测速度,配合机械手自动去重系统,使产品合格率稳定在99.98%以上。这种全自动化解决方案正在推动电动汽车核心部件的智能制造升级。
精密机床主轴动态平衡校正系统开创了加工精度的新纪元。通过实时监测切削过程中的动态失衡,系统可自动调整配重块位置,将主轴径向跳动控制在0.5μm以内。某高端数控机床经优化后,加工表面粗糙度改善40%,刀具寿命延长3倍。
三、技术发展的前瞻视野
新一代设备正在探索量子传感技术的应用可能,超导量子干涉器件(SQUID)的引入,使纳米级振动检测成为现实。这种突破将推动微机电系统(MEMS)制造进入亚微米平衡时代,为微型无人机旋翼、医疗机器人关节等微纳器件提供技术支持。
工业物联网架构下的智能诊断系统正在形成网络化监测能力。云端大数据平台可同时处理上千台设备的振动特征谱,通过机器学习建立故障预测模型。某轴承生产企业应用该技术后,设备突发故障率下降75%,维护成本降低40%。
绿色工业理念驱动下,新型环保校正技术正在替代传统去重工艺。非接触式激光平衡系统通过选择性材料沉积实现质量补偿,整个过程无切削废料产生。这种可持续技术已成功应用于卫星惯性轮制造,使航天器部件的使用寿命延长至15年。
站在工业4.0的转型节点,动平衡测定测试仪已超越单纯的检测工具定位,演变为智能制造体系的核心质量控制器。其技术进化轨迹与工业发展需求深度耦合,在提升设备可靠性的同时,正在重新定义精密制造的品质标准。随着新材料与人工智能技术的持续融合,这项技术必将在高端装备制造领域创造更多可能。
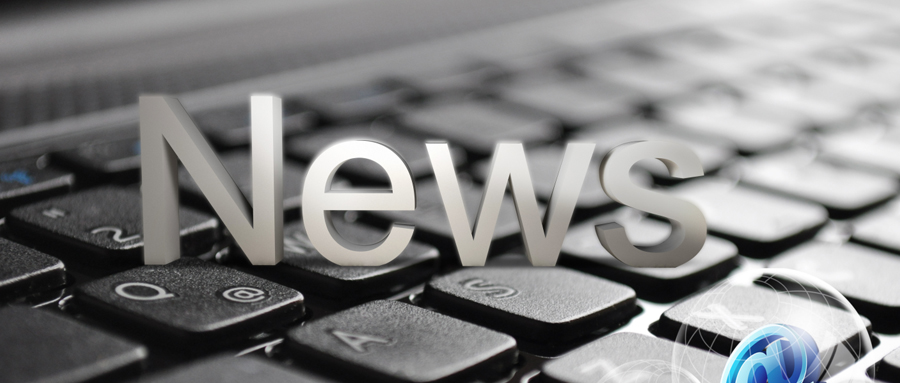